The Right Solution for Every Situation
Insulation materials
Insulation materials made from mineral wool, wood fiber, and cellulose help to boost the energy efficiency of buildings. Whatever type of insulation material you need: Grenzebach supplies the production technology. Our systems help you do everything - from manufacture through to processing and finishing. We supply individual components as well as complete production lines.
From planning to implementation: Grenzebach supplies complete production lines for innovative products from raw panels manufacturing to warehouse. Our customers value the solid, user-friendly technology and the high degree of automation. Grenzebach possesses the know-how of an internationally active equipment manufacturer, also encompassing consulting, engineering, and project management services - a real boon for the insulation materials industry.
Here You Will Find:
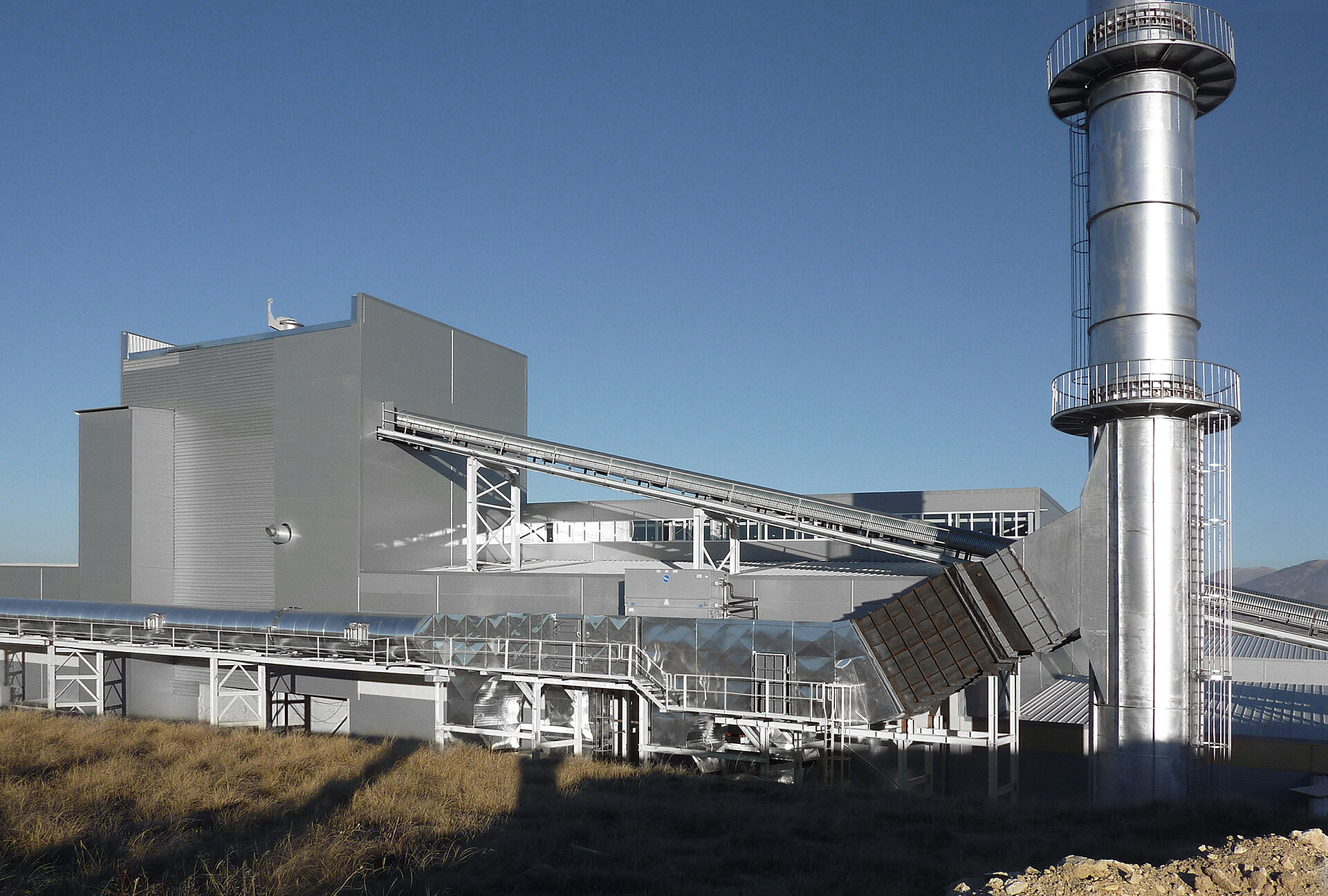
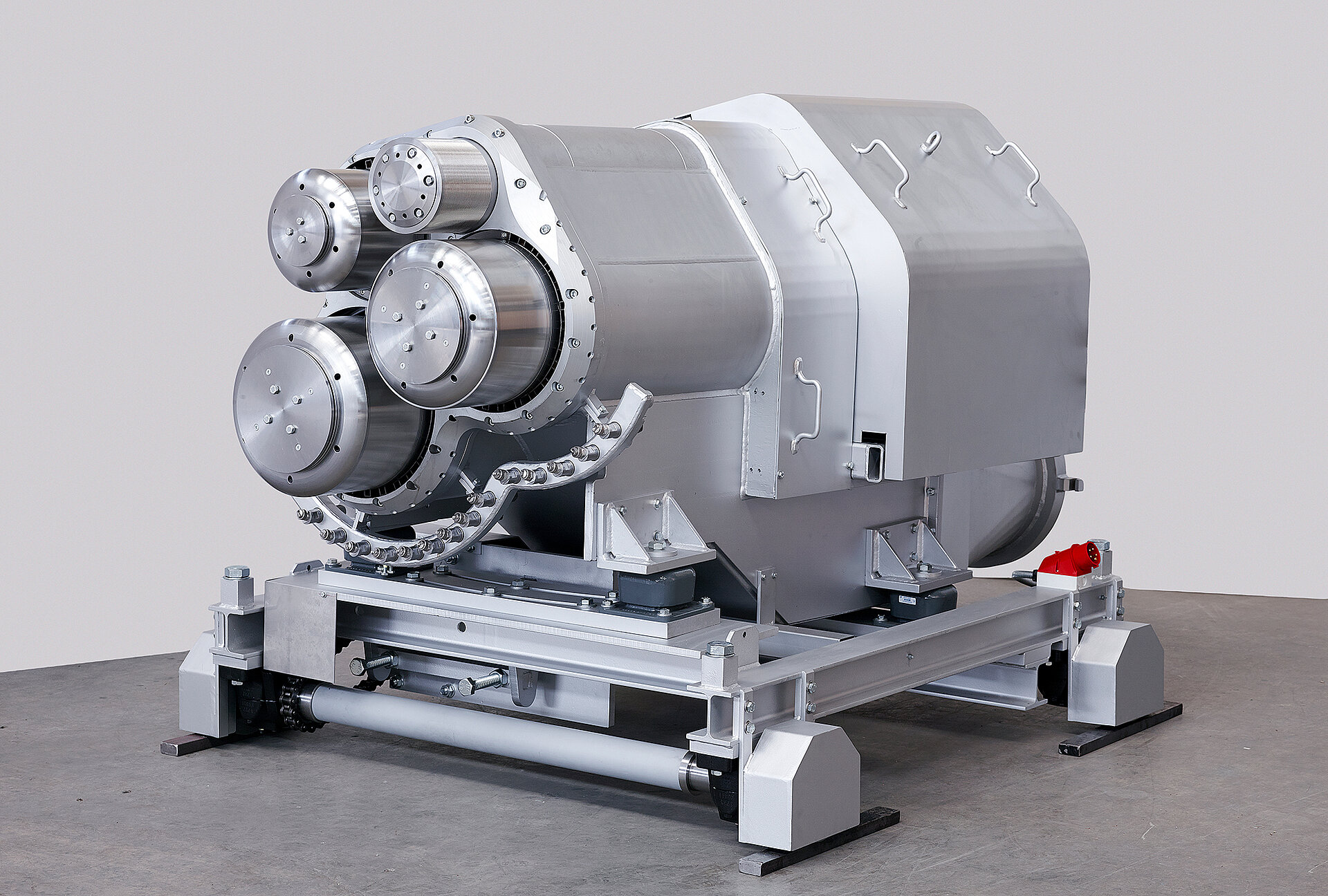
Drying and handling technology for a variety of building materials applications, such as acoustic ceiling tiles, are just as much part of the Grenzebach range as are special processing solutions for value-added products. We are well-versed in high performance lines with a special focus on efficiency and availability as well as the integration of already available equipment.
The building materials industry values Grenzebach's production technology since we are able to respond to individual requirements.
Mineral Wool Production
Complete production line
Panels and mats, laminated or unlaminated with fleece, film, paper, with or without coating - when it comes to the manufacture and processing of mineral wool, Grenzebach offers the full range.
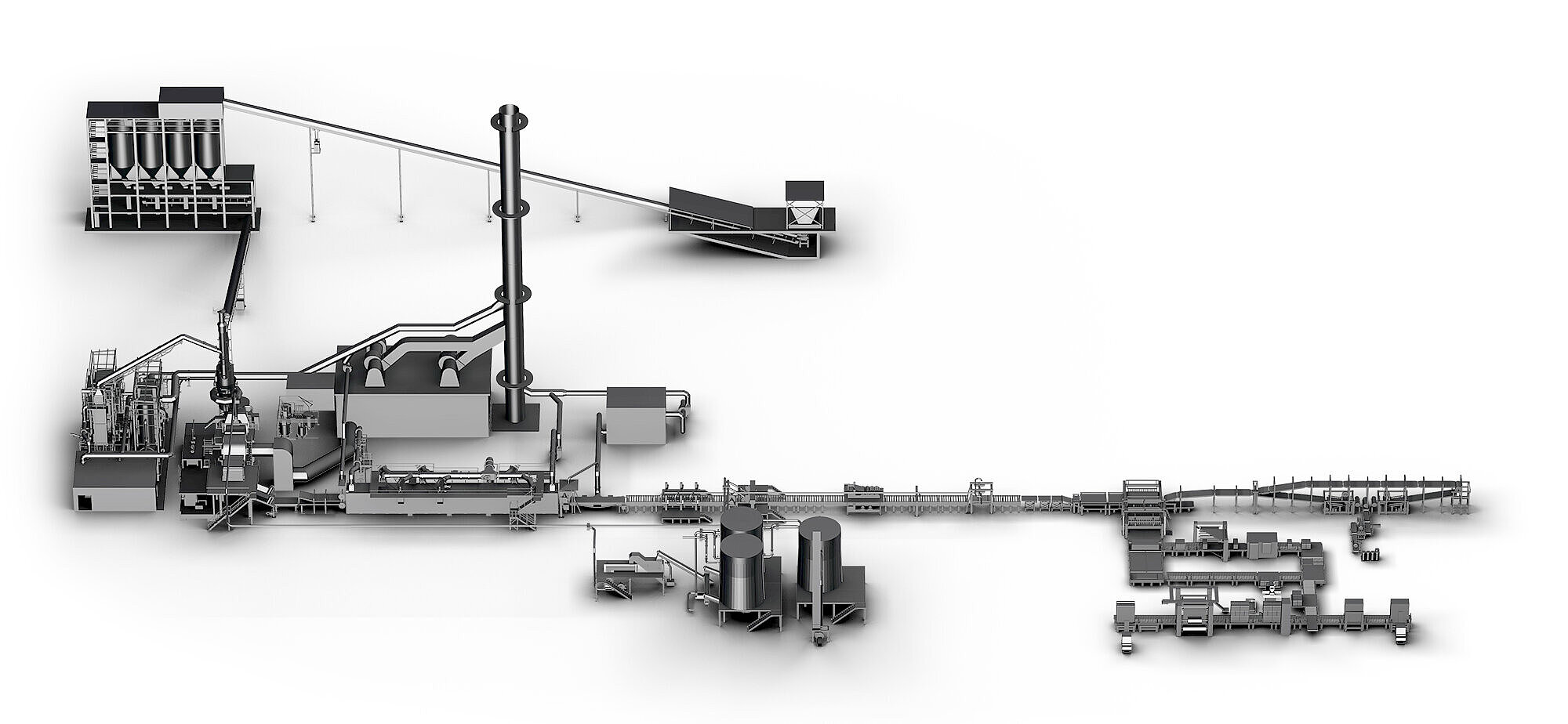
Raw material bunker
Cupola furnace
Spinning machine
Exhaust air cleaning
Collection drum
Pendulum unit
Compression unit
Curing oven
Cooling zone
Exhaust system
Recycling plant
Trim line
Receiving bunk
Stacker
Board line
Roll line
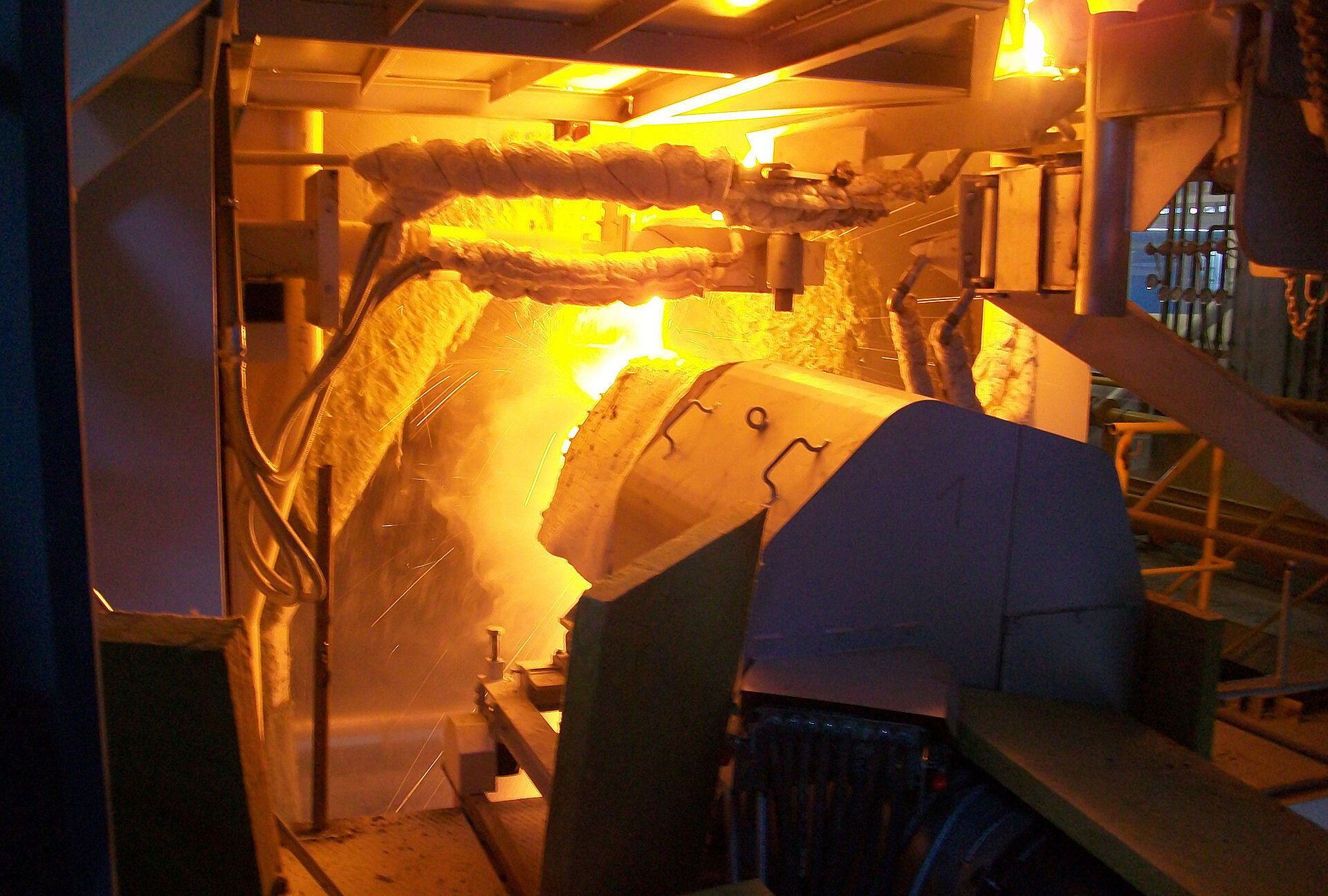
Hot End
The mineral wool itself is manufactured in the hot-end section, which includes everything from raw material handling to cooling of the endless mineral wool strand:
- Raw material handling and treatment systems
- Batch feeding systems
- Cupola furnaces with heat recovery and thermal waste gas incineration
- Binder systems
- Spinning machines
- Drum collectors
- Pendulum units
- Compression units
- Curing ovens with thermal waste gas incineration system
- Cooling zones
- Plant control systems with process visualization
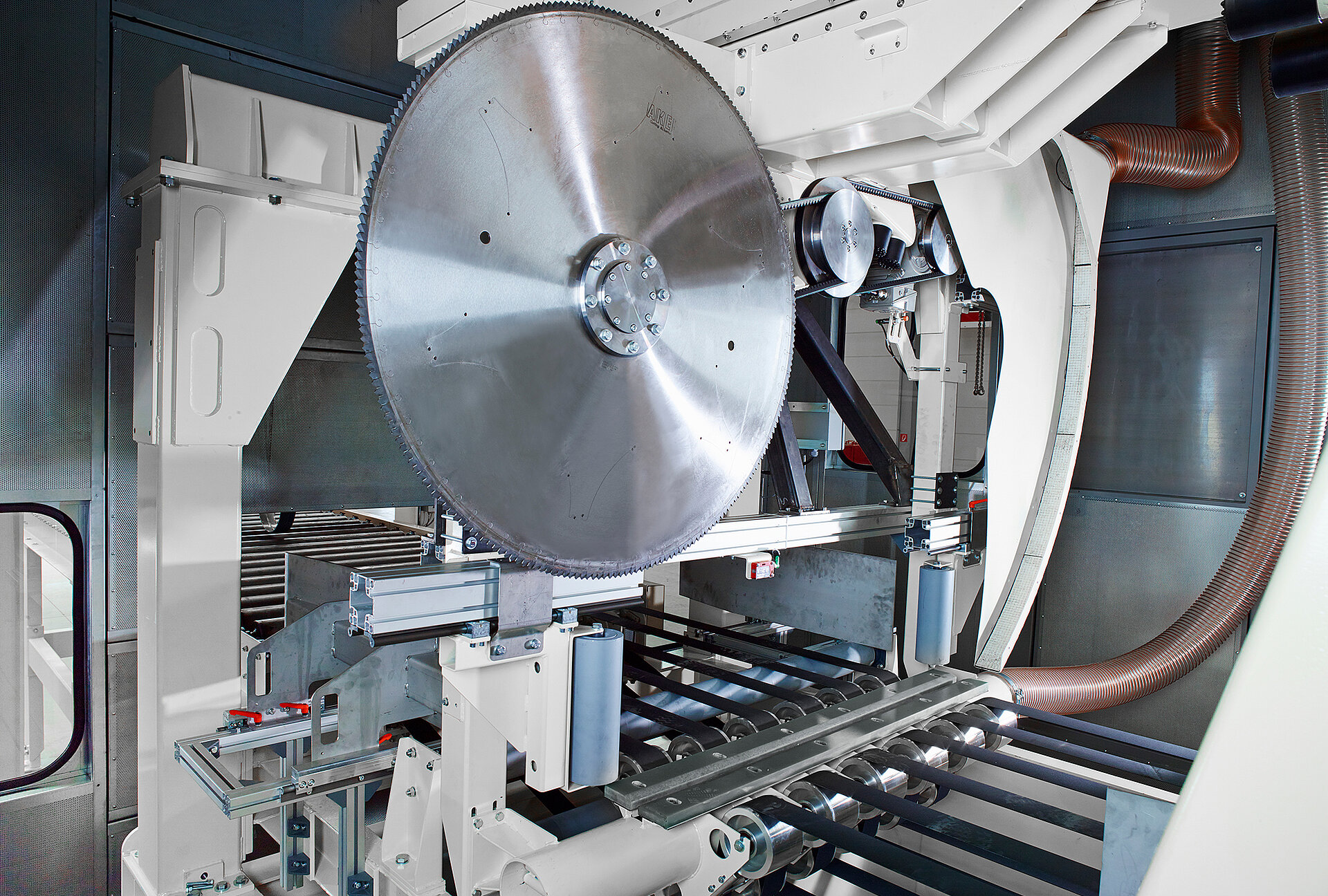
Cold End
In the cold-end section, the mineral wool strand is processed and finished to produce marketable end products that are packed and palletized:
- Sawing
- Stacking
- Packing
- Palletizing
Production of Wood Fiber Insulation Panels
Complete production line
Ecofriendly insulation materials have never been more in demand. Grenzebach supplies all the technology you need to manufacture insulation panels from defibrated woodchips or sawing residue.
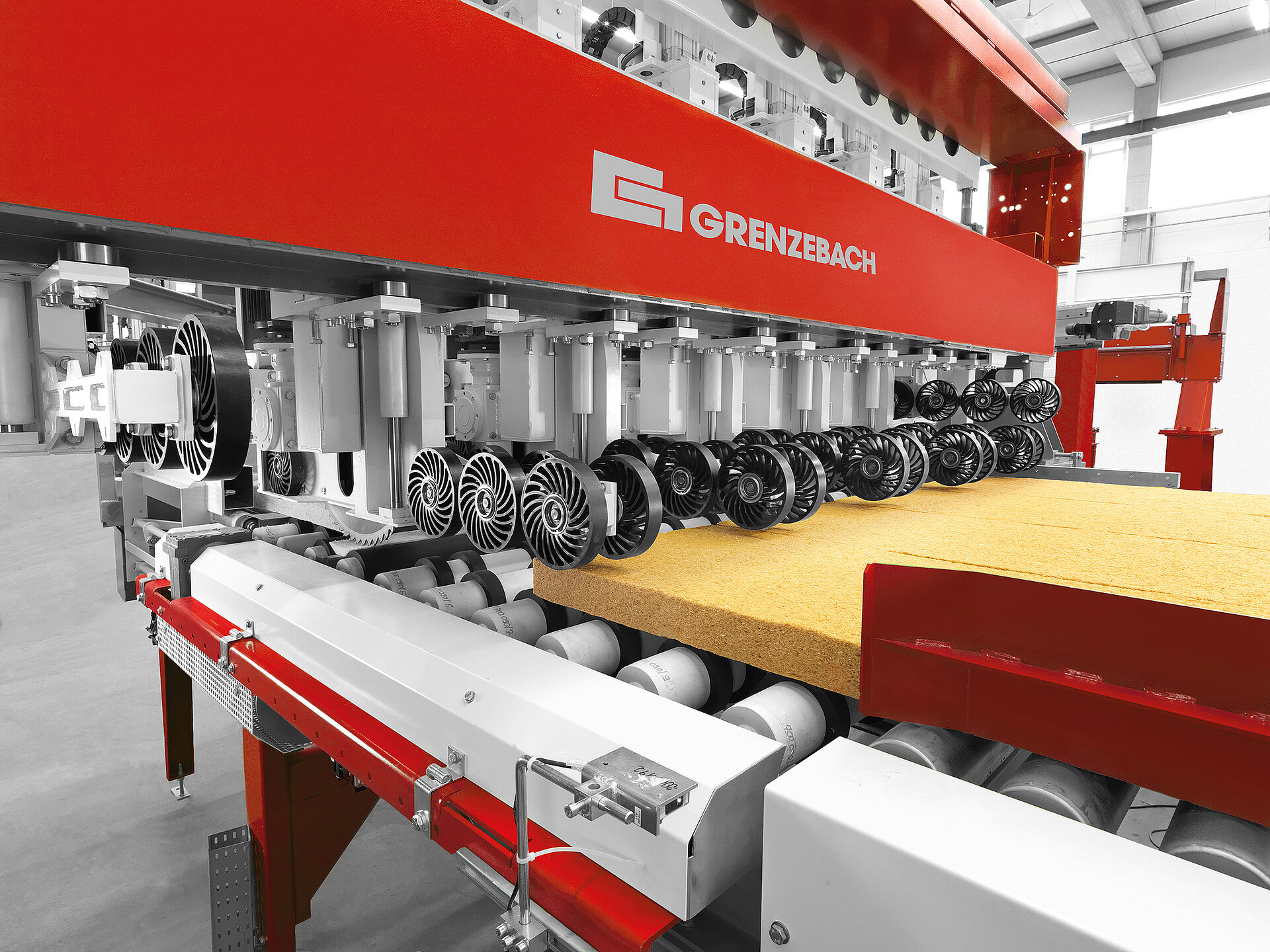
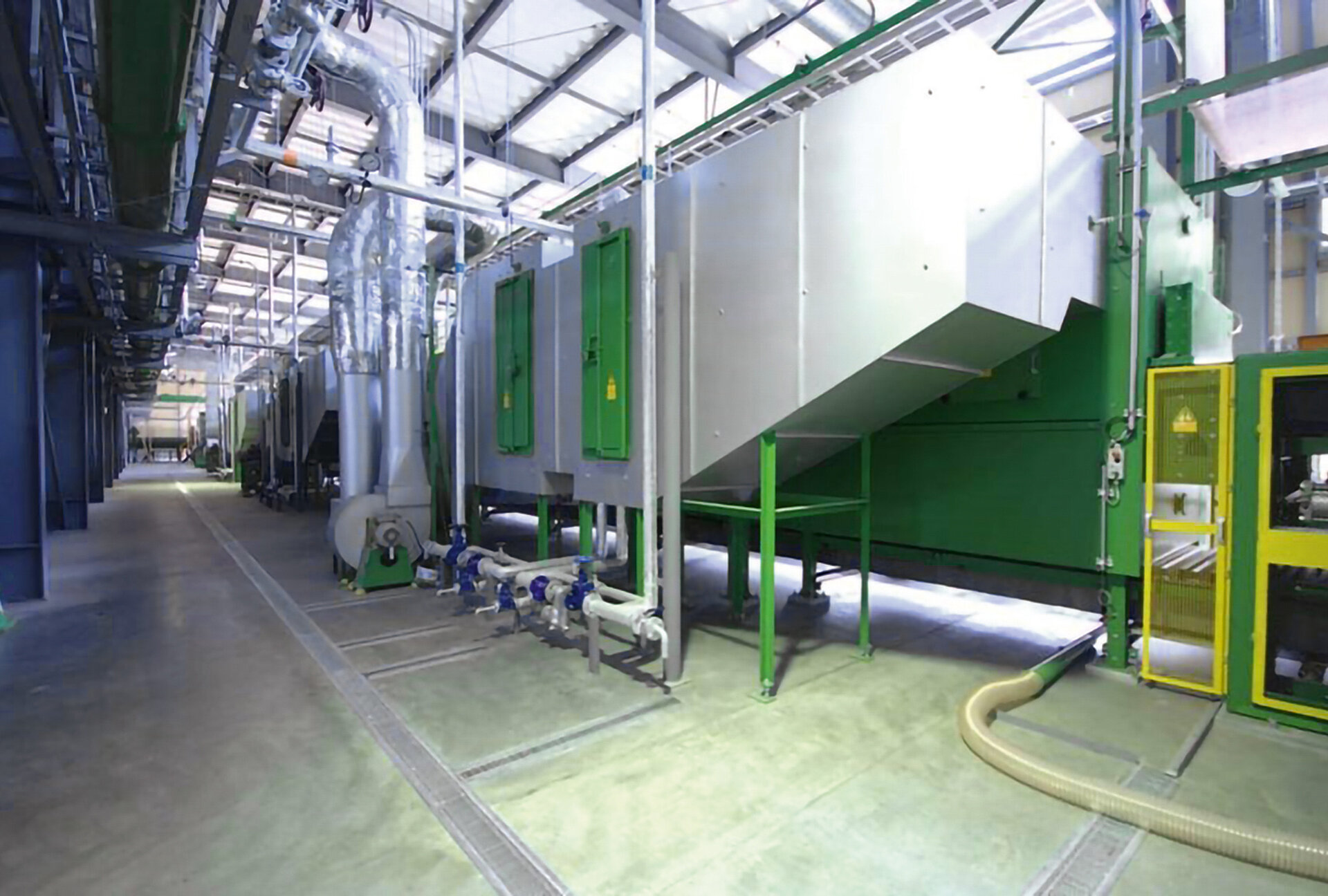
The options and scope of delivery range from fiber preparation to the cut and packaged product. Key components here include fiber dosing and mixing systems and the flexible curing oven. Our systems manufacture high-quality, ecofriendly, and easily installable insulation materials for buildings. Grenzebach supports the entire process - resulting in wood fiber insulation panels offering optimal thermal insulation.
Line for Flexible Wood Fiber Insulation Boards for ZIEGLER GROUP in Record Time
SUCCESS STORY
The start of wood fiber insulation board production by ZIEGLER GROUP's naturheld GmbH, a company explicitly launched for that purpose, marks another step towards a 100 % ecological wooden house. The innovative production line for flexible wood fiber insulation boards was planned and built by Grenzebach in a record time of twelve months – providing naturheld with the highest-capacity plant on the market immediately upon start-up.
Production of Cellulose Insulation Material
Complete production line
From newsprint to blow-in insulation material: In buildings in particular, cellulose offers clear advantages over mineral‑based insulation materials. Thanks to its heat storage capacity, cellulose insulation material prevents living areas from becoming too hot in the summer months. Europe's leading manufacturers of cellulose insulation material rely on our system components because of their outstanding results.
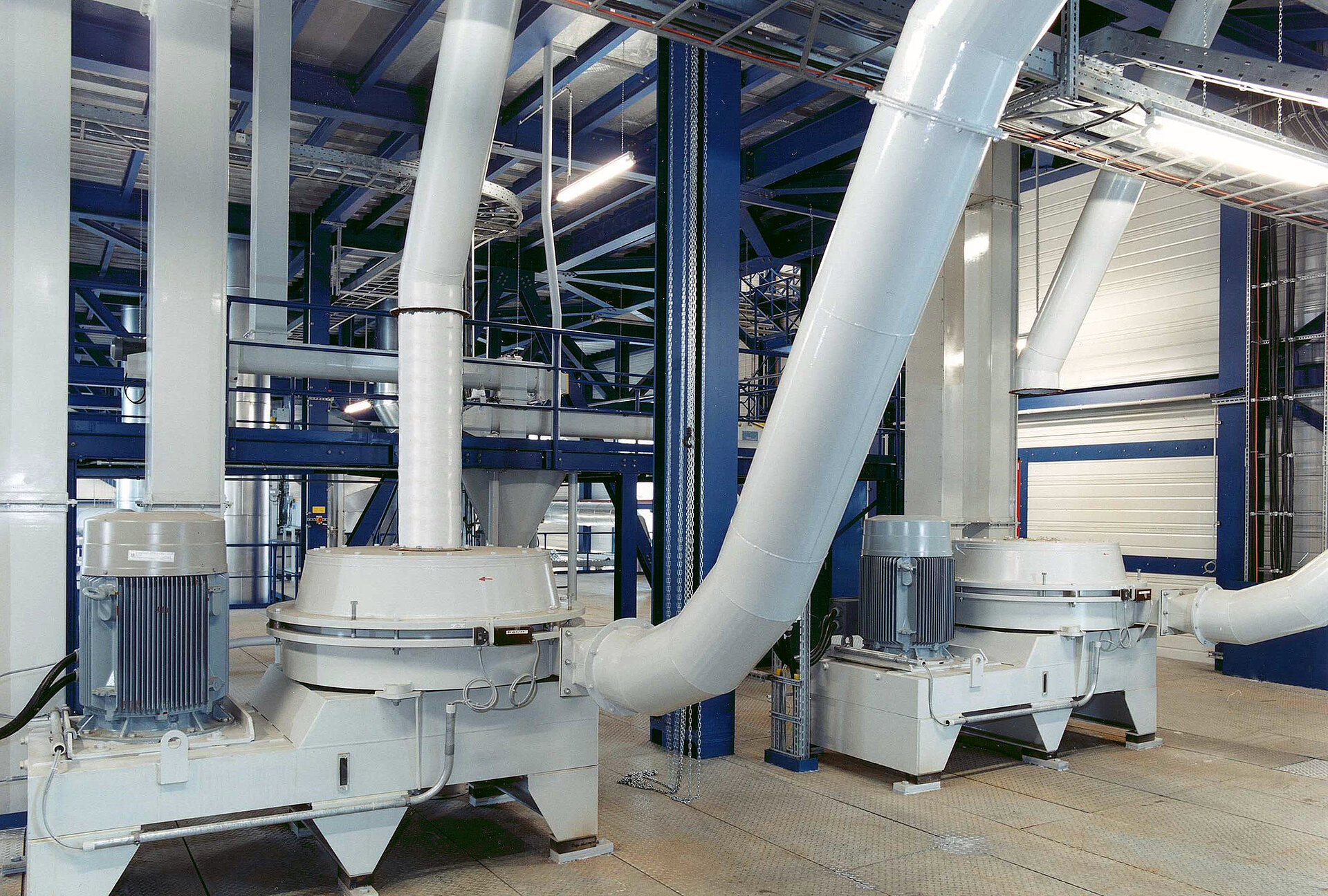
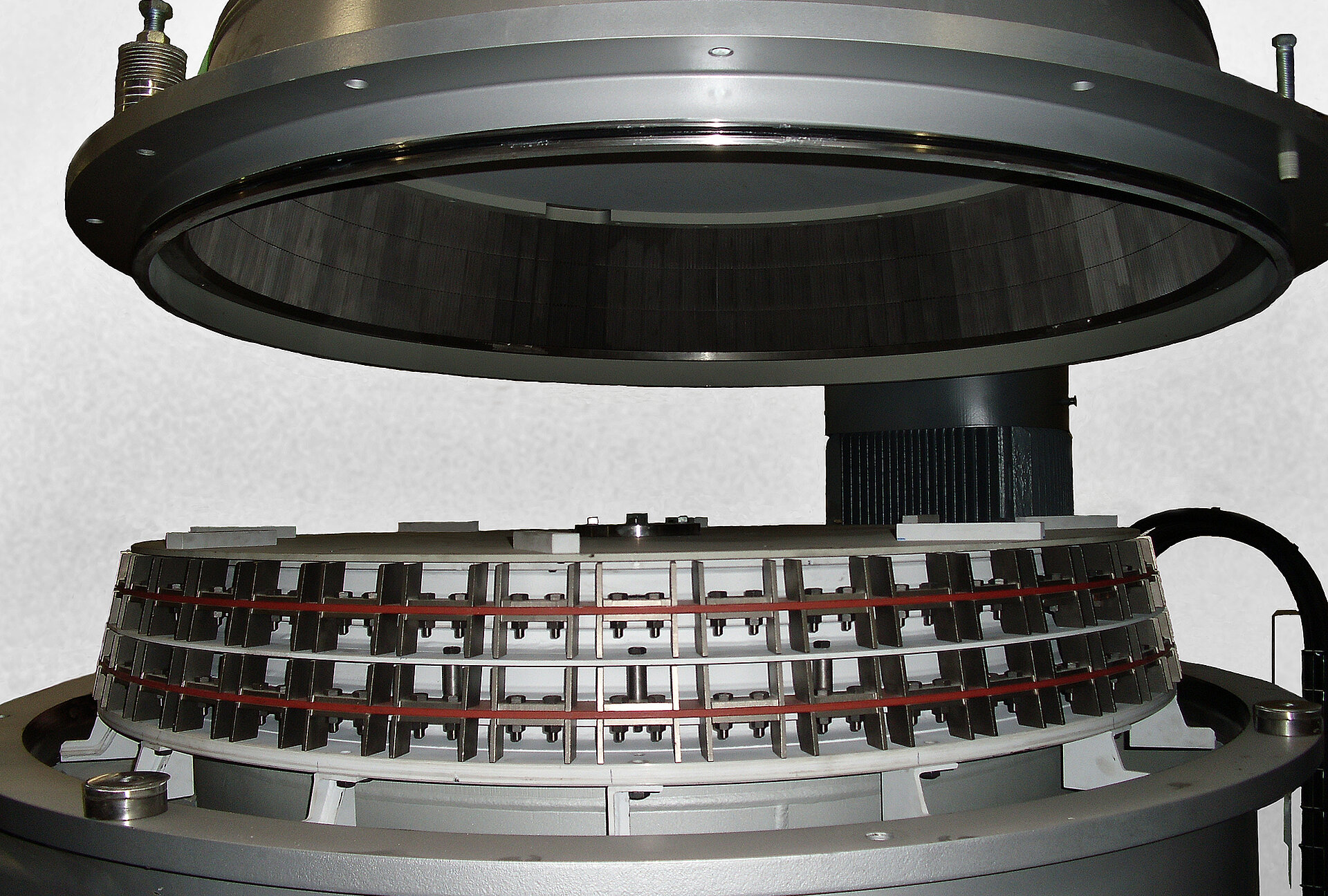
The centerpiece of the system is the whirlwind mill, which defibrates the old, recycled paper to create cellulose insulation material. In the whirlwind mill, the flame retardant is also applied to the individual insulation material fibers. A pneumatic system then discharges the defibrated paper from the mill to a separator where the fibers are separated from the air. The finished cellulose insulation material is then sent to the weighing and packing station.
Your Contact Persons
Whether producing organic insulation materials or conventional, fire-resistant insulation materials: We are looking forward to talking with you about your requirements and desires.
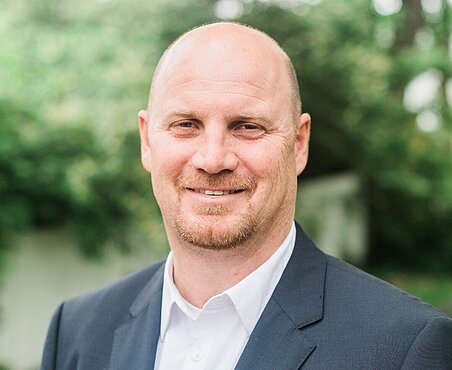
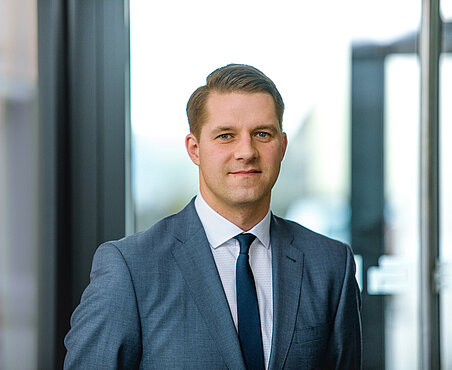