A Weld Seam That Doesn’t Look Like a Weld Seam!
Welding – loud and dirty, right? Not friction stir welding! Heat makes the material deformable, and a rotating tool stirs the material at the seam. In this way, FSW technology creates a homogeneous structure with outstanding properties. The whole process is emission-free!
When a weld has to be really tight, FSW is the method of choice. It joins workpieces in a reproducible pressure- and media-tight manner. FSW can be optimally integrated into industrial series production. The result is top quality that is easy to reproduce. Friction-stir-welding technology – an investment that will pay off!
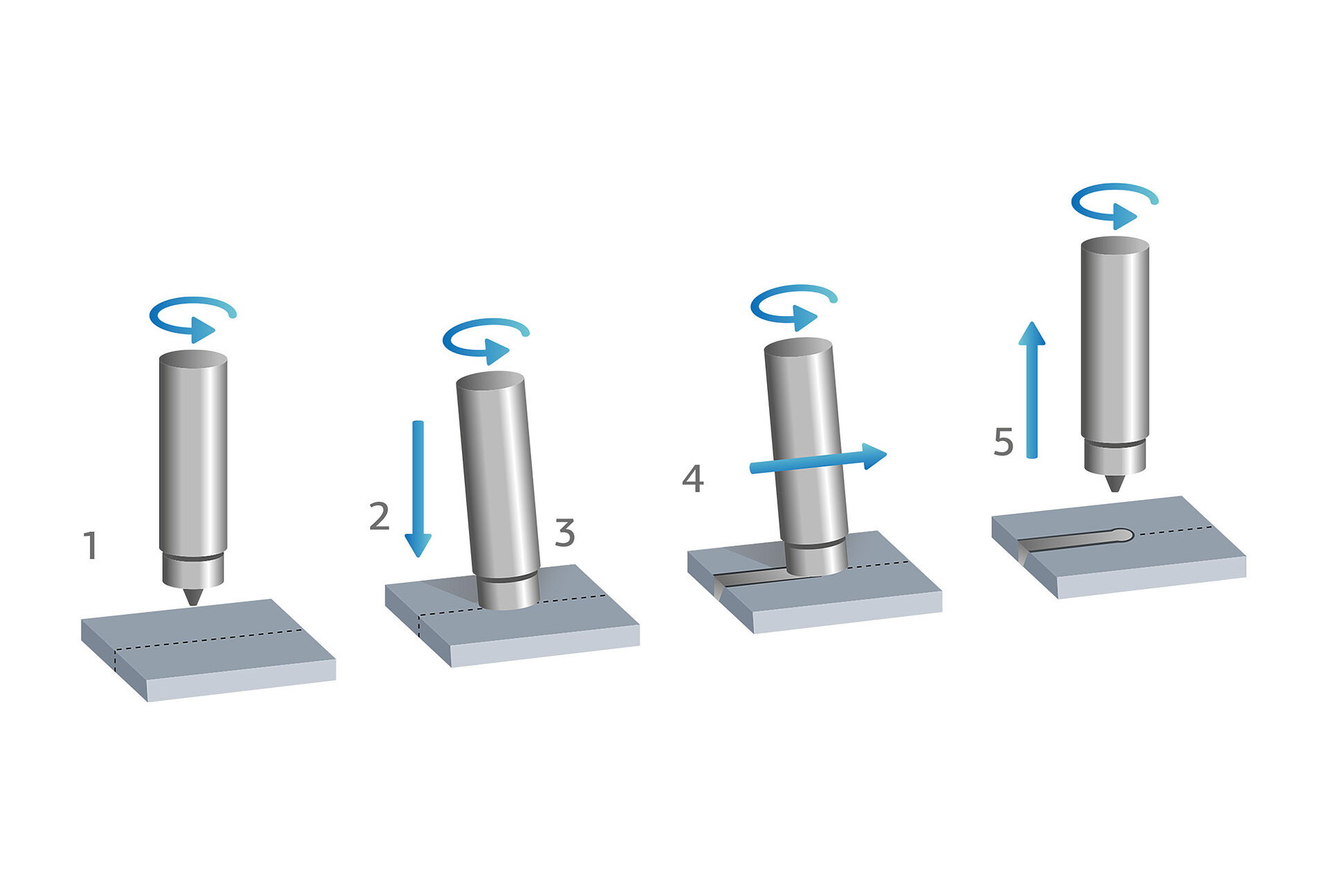
How Does Friction Stir Welding Work?
This is how FSW technology works, step by step:
1. Rotating welding tool
A wear-resistant tool is set in a spindle and rotates.
2. Immersion & 3. Tilt angle 0 - 5°
The tool dips directly into the weld seam and tilts to an angle of 0 - 5° and generates heat through friction.
4. Feed
The material becomes malleable and is stirred by the tool’s forward progress along the seam.
5. Removal
When the tool is removed from the seam, the result is a firm, media-tight, pressure-proof bond between the two workpieces.
Advantages
- Durable, media- and pressure-tight weld seams
- High, reproducible seam quality
- Low-warpage joints
- No pores or hot cracks
- No emissions and no auxiliary materials such as shielding gas, powder, or welding wire
Take Advantage of Our Equipment and Tool Portfolio!
Friction stir welding – solutions for your specific needs
Explanatory Video Series on Friction Stir Welding
UPDATES & VALUABLE INSIGHTS FROM OUR EXPERTS
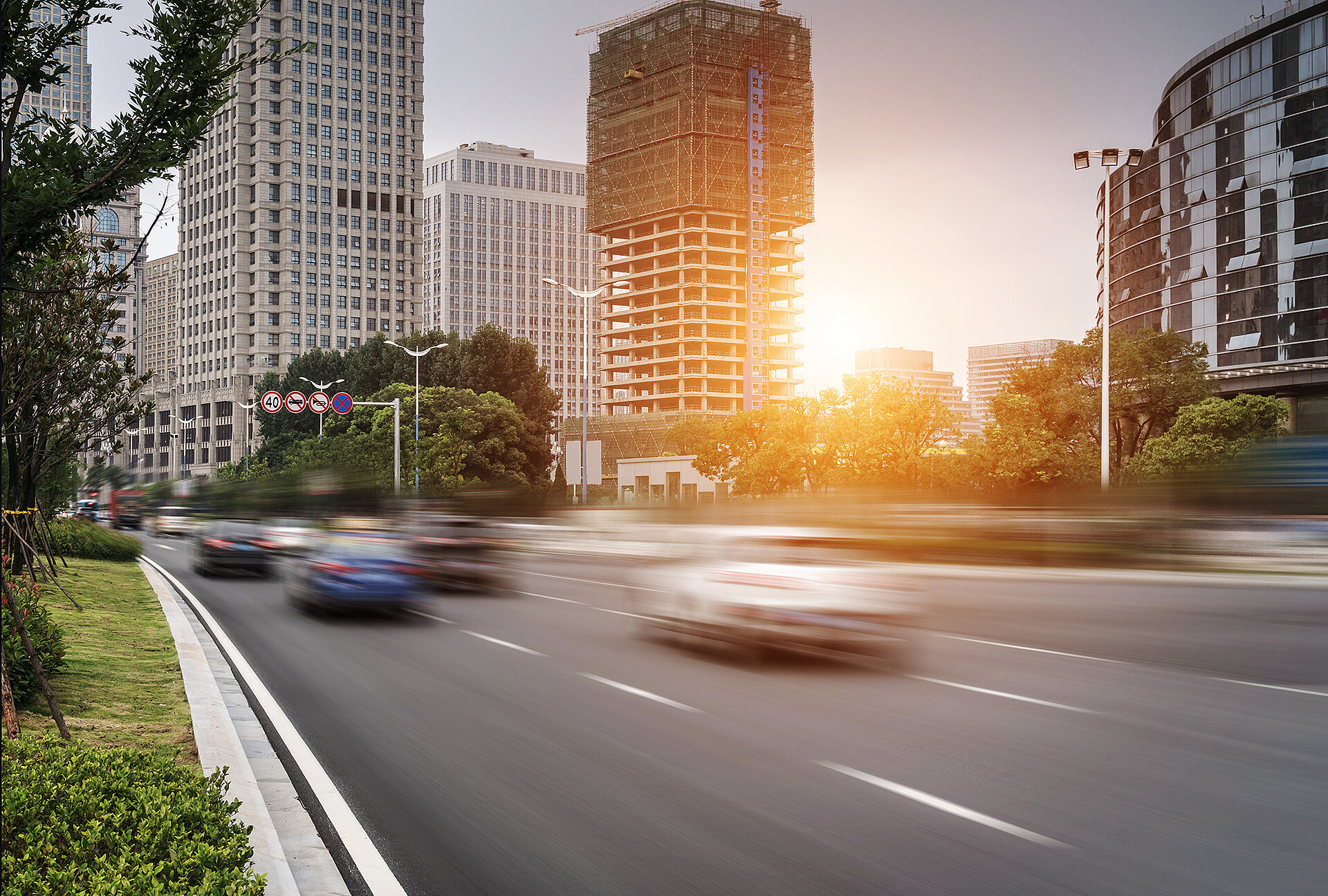
Friction Stir Welding for E-Mobility
Crash-test-safe battery trays and heat exchangers
Technological change has arrived in the automotive industry. Mounting pressure to roll out low-emission vehicles is coming from the political arena.
Concepts such as driving on green energy have direct impact when working with aluminum. Therefore, demand for welding of castings in the automotive industry is skyrocketing.
A good example is manufacturing battery trays and heat exchangers. This is where green energy and green technology meet: friction stir welding is emission-free.
“Providing a comprehensive response to our customers’ questions and concerns has always been our hallmark. The FSW experts at Grenzebach support you with holistic solutions. We also know the limits of the technology – we are the right sounding board if you want to create something new on the basis of experience. From the very first idea, we can advise you on product design and process control, and we offer high-performance equipment to do so.”
For North America
Your Contact Person: John Fluker
Do you have questions about friction stir welding? Would you like to know whether a new idea can be implemented with FSW? Or do you need support in selecting a system? Please contact us. We'll be happy to advise you!
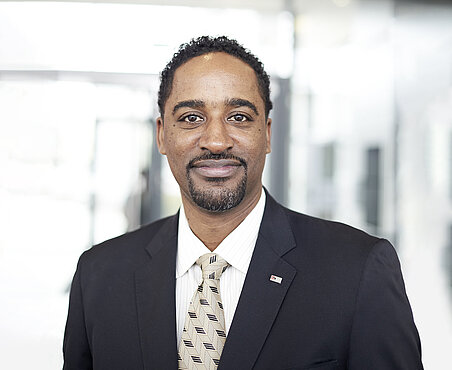
For all other regions
Your Contact Person: Sahin Sünger
Do you have questions about friction stir welding? Would you like to know whether a new idea can be implemented with FSW? Or do you need support in selecting a system? Please contact us. We'll be happy to advise you!
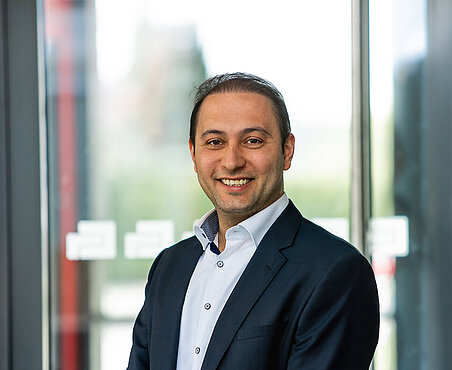
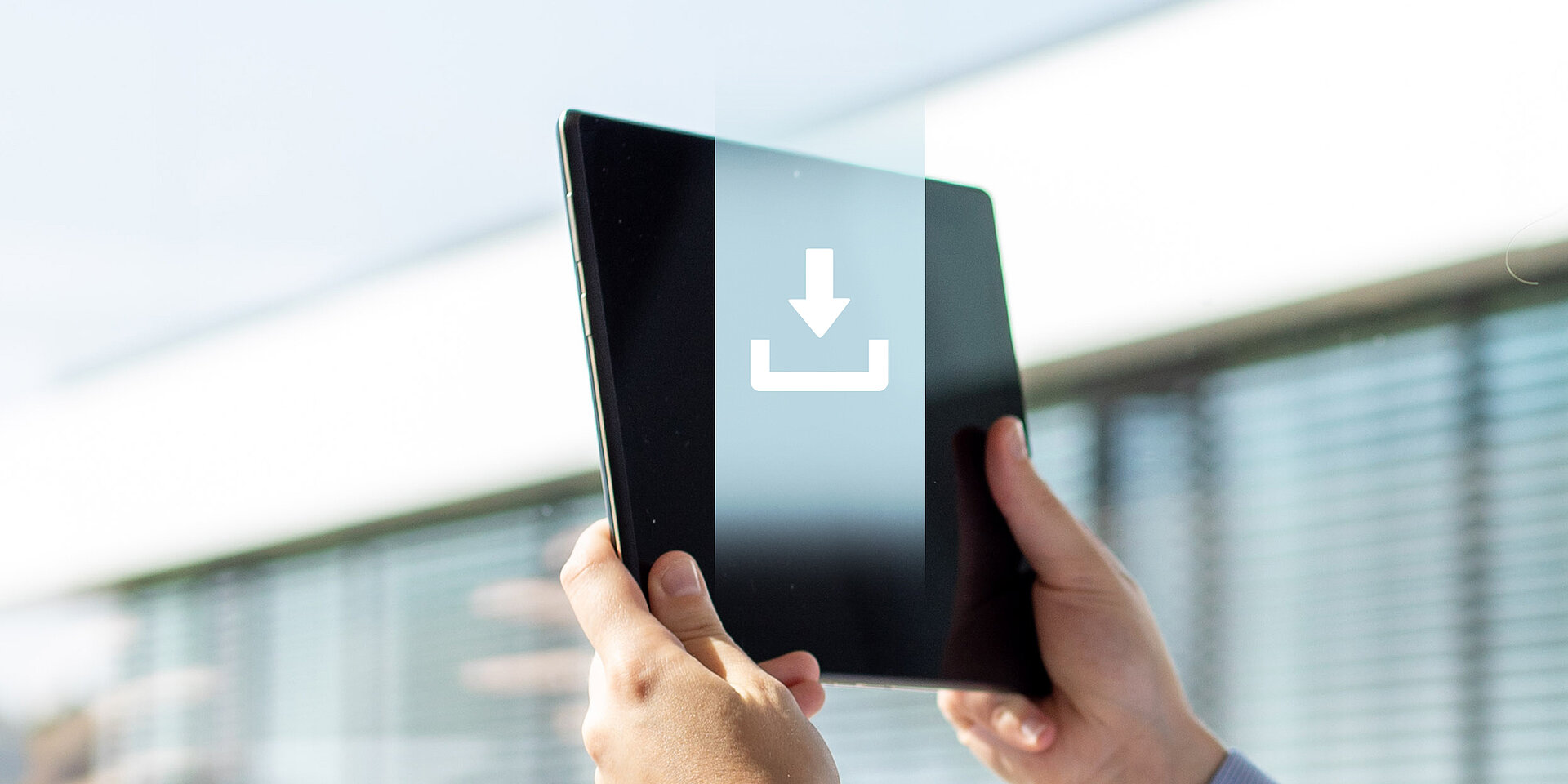
Download & Links
More information