Process Technology – Crucial for Outstanding Powders and Bulk Solids
Process plants
Every day, powders and bulk solids are used in countless products, such as construction materials, plastics, paints, fertilizers, and many others. Process-treated bulk solids are an essential component of numerous materials and are crucial for product quality. To ensure this quality, process technology processes must meet numerous parameters, such as exact particle sizes, particle densities, and residual moisture content (dry substance).
We contribute our expertise and our technologies to ensure that your powders and bulk solids are processed with the best possible quality and process efficiency. Grenzebach works with a holistic approach. We keep different bulk material properties and reaction behaviors in mind.
Our experts have in-depth knowledge of diverse powders and bulk solids used in industry. We support our customers from planning and design to commissioning and maintenance.
Our Experience – Your Success
Our solutions and services incorporate 130 years of experience in the efficient processing of raw materials, dating back to Babcock BSH. Combined with the process and technology knowledge gained in Grenzebach’s 60 years, this means we can apply extensive know-how to your process technology solutions. Our experience guarantees your success.
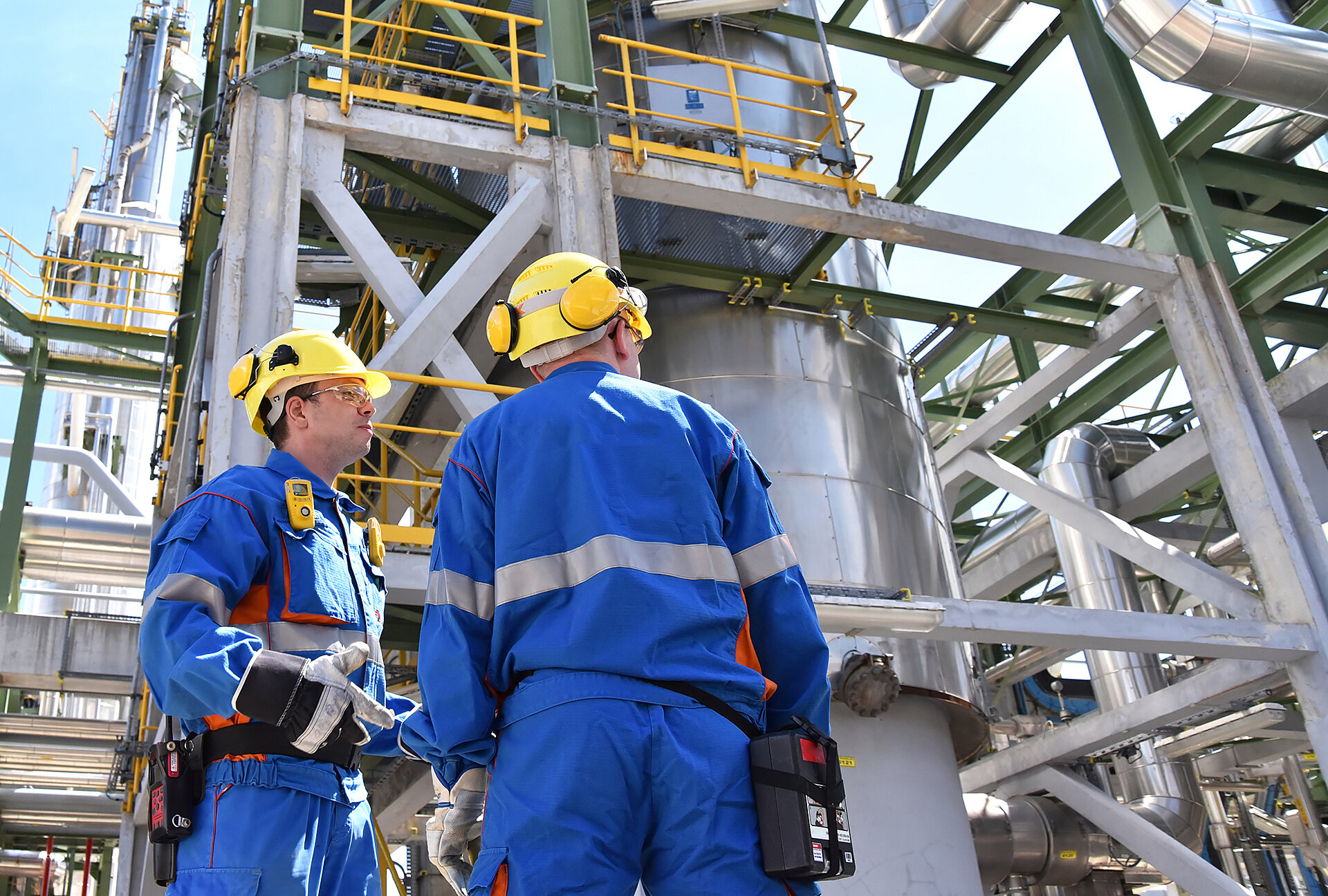
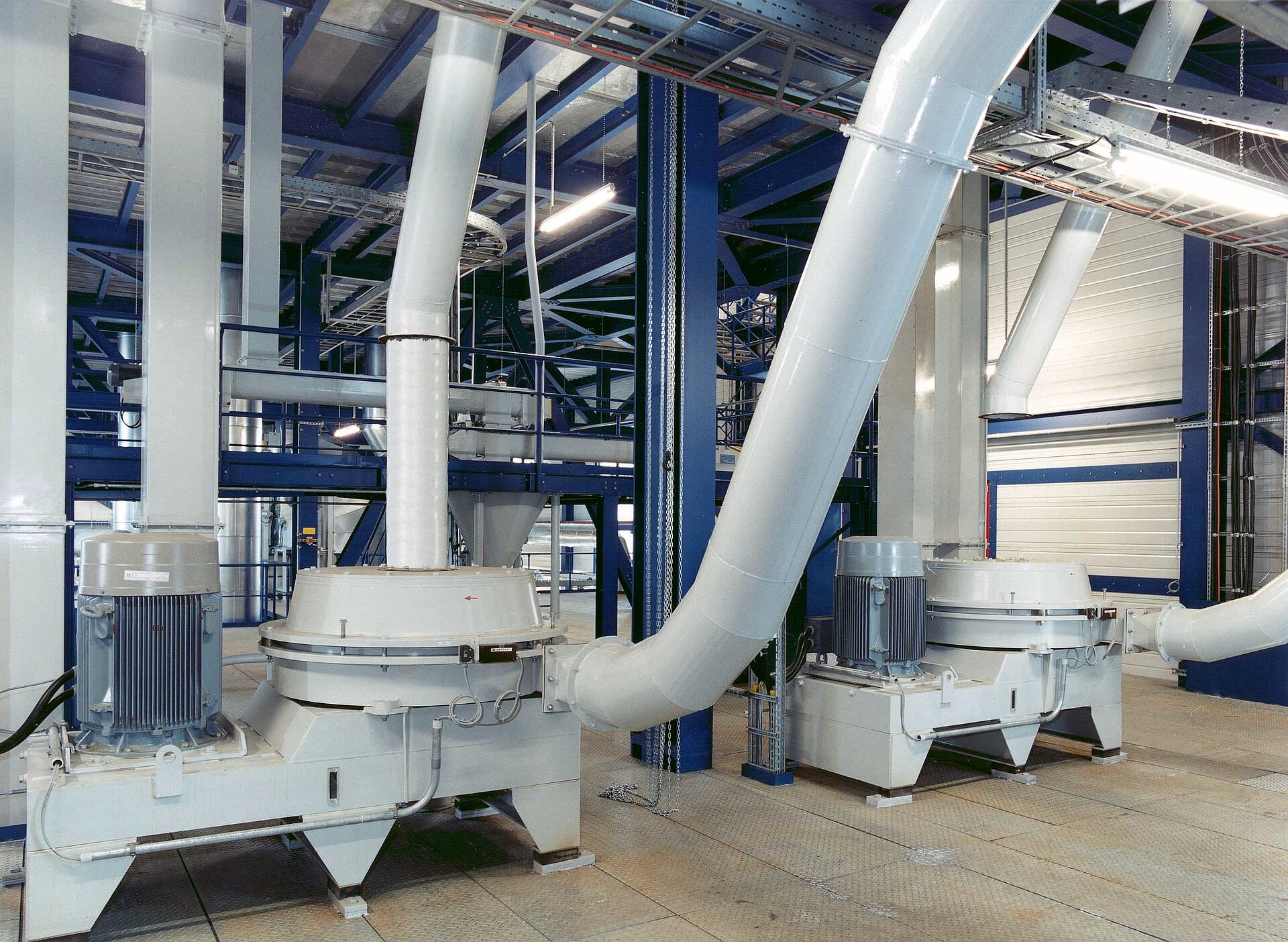
Grinding, Classifying, Compacting
Mechanical Process Technology
Coarse crushing or finest powder grinding? Compacting bulk solids to the highest degree? Classifying bulk materials according to their particle size? Whatever your task, Grenzebach will support you in selecting the optimum process technology. With our proven technologies, we will equip you with a tailor-made mechanical process engineering system.
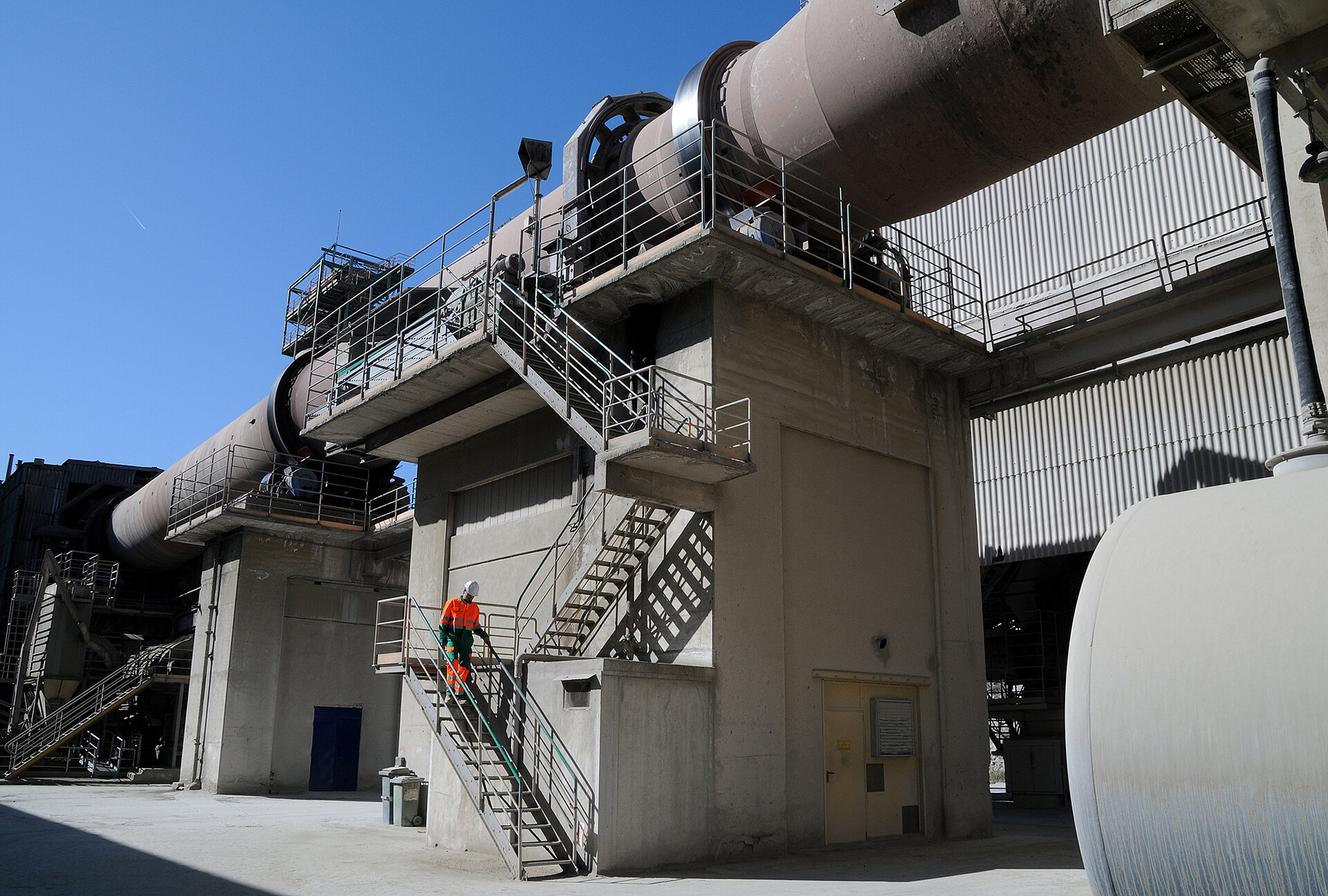
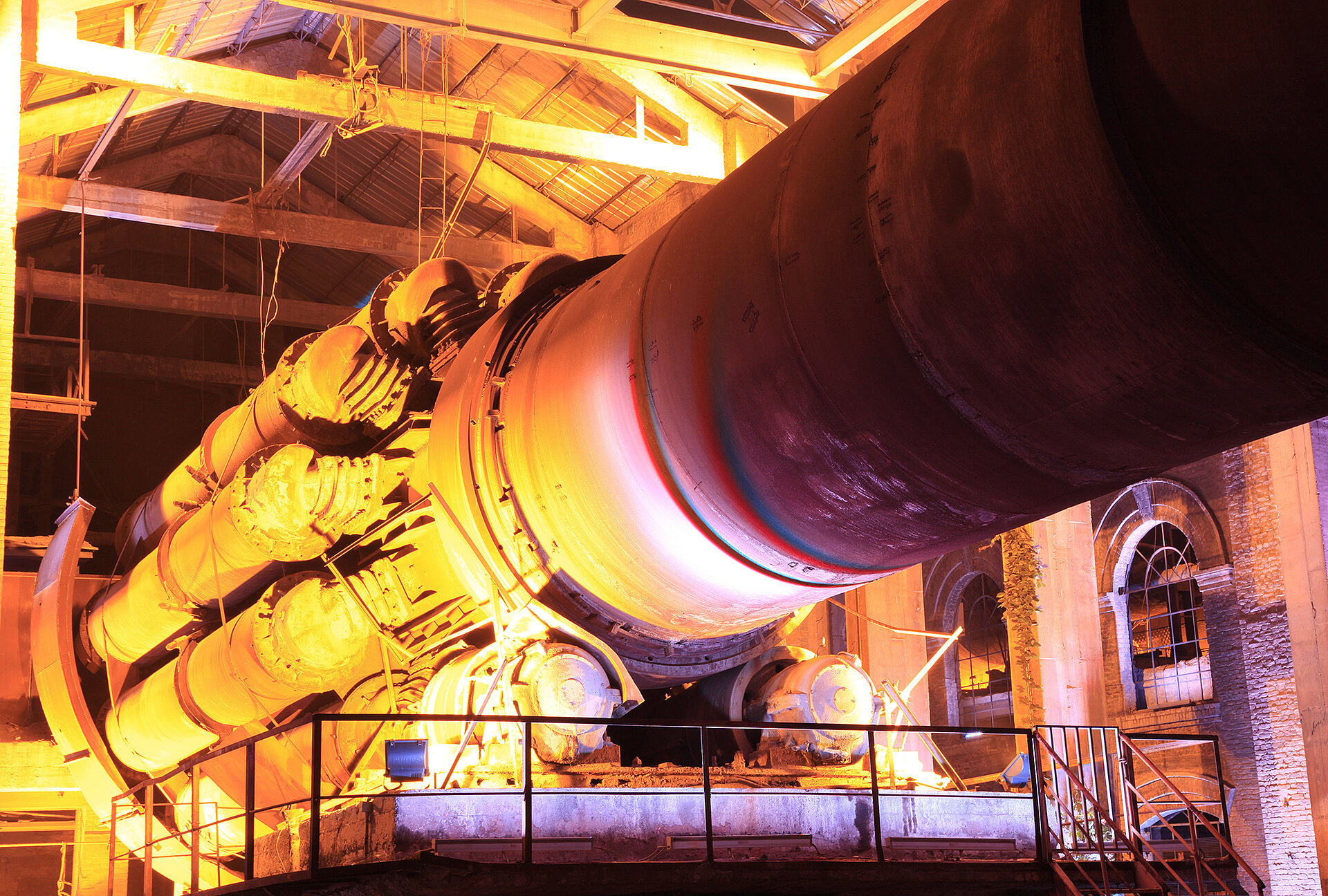
Heating, Cooling and Drying
Thermal process technology
Heating and cooling of fine-grained bulk materials: this is what Grenzebach’s thermal process solutions can deal with. By optimally controlling the temperatures in the individual processes, they make thermal separation processes such as absorption or calcination possible. We make efficient, economical use of the waste heat generated from thermal processes: the heat is recycled and used to temper the bulk materials. This saves resources and improves your carbon footprint!
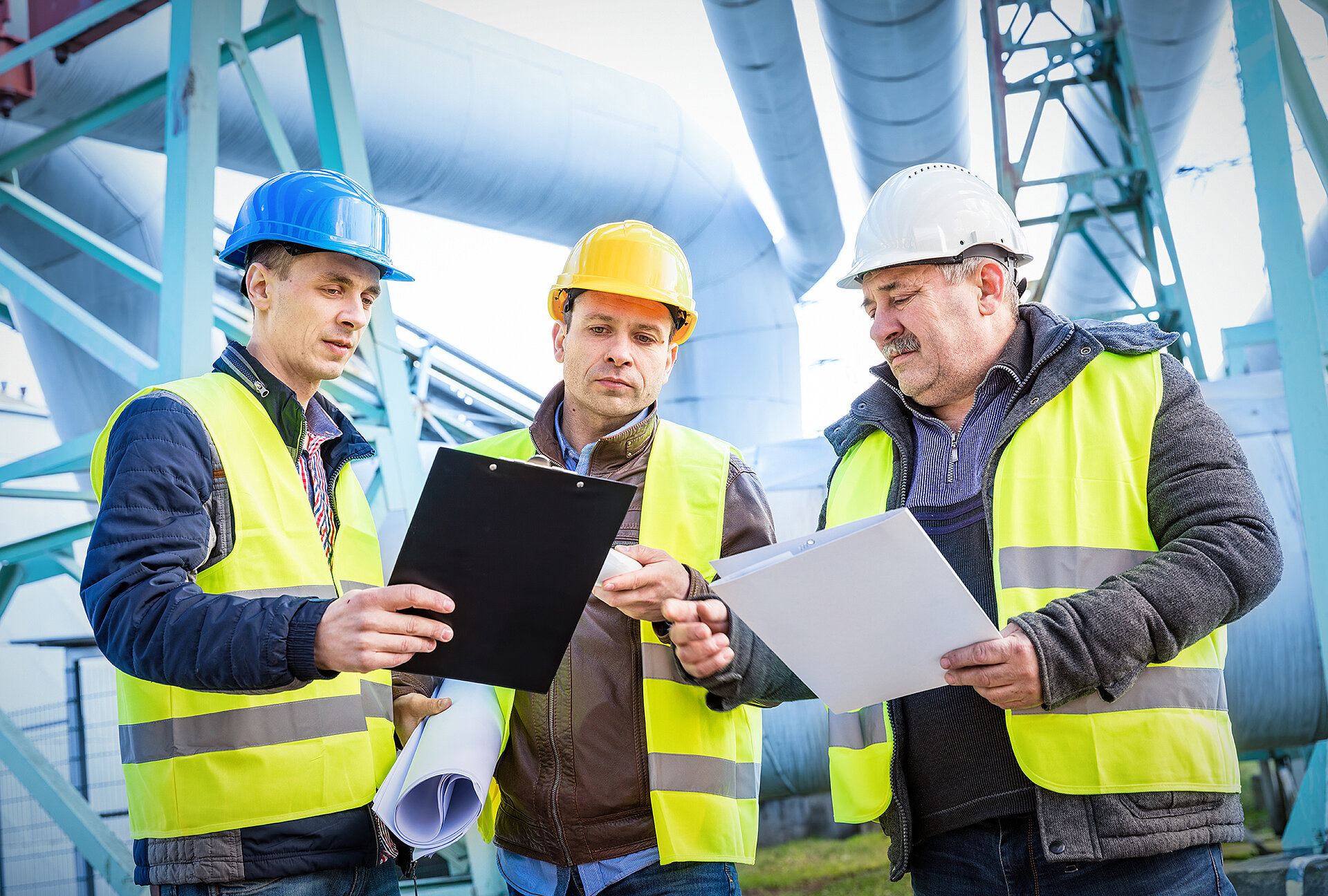
Exploiting Potential with Optimum Process Engineering
Project management to ensure your success
Ensuring high product quality, being able to deliver continuously, and meeting customer needs with maximum process efficiency: these are the requirements that unite companies in numerous industries dealing with powders and bulk solids. The Grenzebach team is your reliable partner.
To ensure that you achieve the best possible results over your plant’s entire life cycle, we get involved in working together at an early stage. At the planning phase, we analyze the material properties of your bulk solids in our own laboratory in Bad Hersfeld. Based on the knowledge we gain, we create your tailor-made solution for process engineering.
You may also have questions about tomorrow and the day after: How can materials be processed in a more product-friendly way? How can process plants work even more energy-efficiently? Grenzebach’s experts can provide answers for process optimization here, too.
Analysis Service and Feasibility Tests
- Analysis of bulk material properties, such as material characteristics, bulk density, particle size and other parameters
- Feasibility test under realistic conditions in Grenzebach’s technical center
- Preliminary test for special requirements; integrated into your research and development
Layout and Integration into Your Process Environment
- Defining parameters and designing the equipment accordingly.
- Scaling of the equipment
- 3D scanning of your operating environment
- Technical solutions for integration of upstream and downstream process steps
Commissioning and Assembly
- Worldwide assembly and commissioning by Grenzebach experts on site
- Training and instruction of your employees
Contact
Your Contact Person: Michael Meyer
From special solutions for processing your products to questions about existing plants: feel free to contact us with your process engineering concerns!
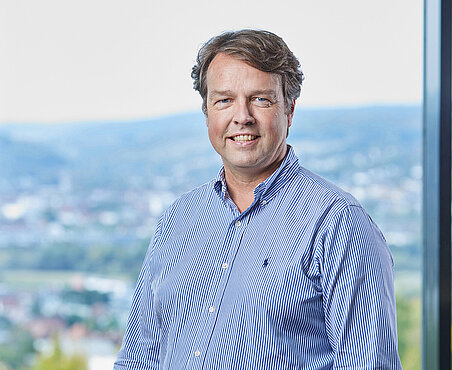