The double spindle FSW machines of the new D-DSM series enable boost the productivity
Nuremberg, Linz, Nashville: Grenzebach present the new Friction Stir Welding systems of the D-DSM series at three exhibitions.
With the recent extension of the machine portfolio for Friction Stir Welding (FSW) technology, Grenzebach enables the user to achieve a significant boost in productivity: With the innovative double spindle FSW machines of the D-DSM series (D-DSM: Double Spindle Dynamic Stirring Machine) two independent operating welding heads are available to the user by adding a second gantry.
“The effective cycle times can be significantly reduced with the new D-DSM double spindle systems. Users of the Friction Stir Welding technology can increase their productivity enormously at constant high quality level of the joining results due to our portfolio extension” says Sahin Sünger, Product Manager for Friction Stir Welding technology at Grenzebach.
Two-sided loading of the workpieces
Grenzebach, as an experienced system integrator and supplier of Friction Stir Welding equipment, delivers turnkey FSW process solutions for industrial serial production and works continuously on innovations.
With the D-DSM series, companies can tap into economic potential, especially with large production volumes. Sahin Sünger explains „Due to the higher efficiency in the production use, the demand for systems and equipment is reduced considerably, the required total investment decreases significantly”.
For even greater efficiency, the D-DSM series also features a two-sided workpiece feeding system, which allows a cycle time concurrent loading of the machine.
Highest Quality with DynaSTIR
FSW technology provides durable, strong, media and pressure tight joints. Friction stir welding as a solid state welding process does not produce any pores or hot cracks. These are exactly the effects that often lead to leaks in conventional fusion welding. The highest quality is provided by the DynaSTIR tooling technology from Grenzebach, which reduces the process forces up to 50 percent compared to conventional FSW tools and thus enables gentle component processing. Furthermore, the heat input is lower. Therefore, less distortion arises and the components remain dimensionally stable.
Demanding Components
Friction stir welding is used in numerous industries due to its various technological advantages nowadays: From the automotive industry with demanding components such as heat exchangers or battery to consumer electronics. Highest tightness with even lower cycle times: Anyone who wants to get an idea of the latest Grenzbach portfolio enhancements regarding the FSW technology will have the opportunity at three major trade exhibitions in the summer and autumn of 2019:
- Nuremberg: Automotive Engineering Expo from June 4th to 5th, 2019; hall 12, booth 419
- Linz: Schweissen from September 10th to 12th, 2019; booth 411
- Nashville, USA: Aluminium USA from September 12th to 13th, 2019; booth 708
Professional sparring included
Before, during and after the exhibitions: Our experts are pleased to assist you with technical discussions of your specific joining concepts. Even during the design phase of the components, Grenzebach supports with a FSW-specific design of assemblies.
Sünger emphasizes: "A cooperative partnership and an intensive professional sparring with our customers are particularly important to us. We take the individual requirements from practice to further advance the FSW technology.“
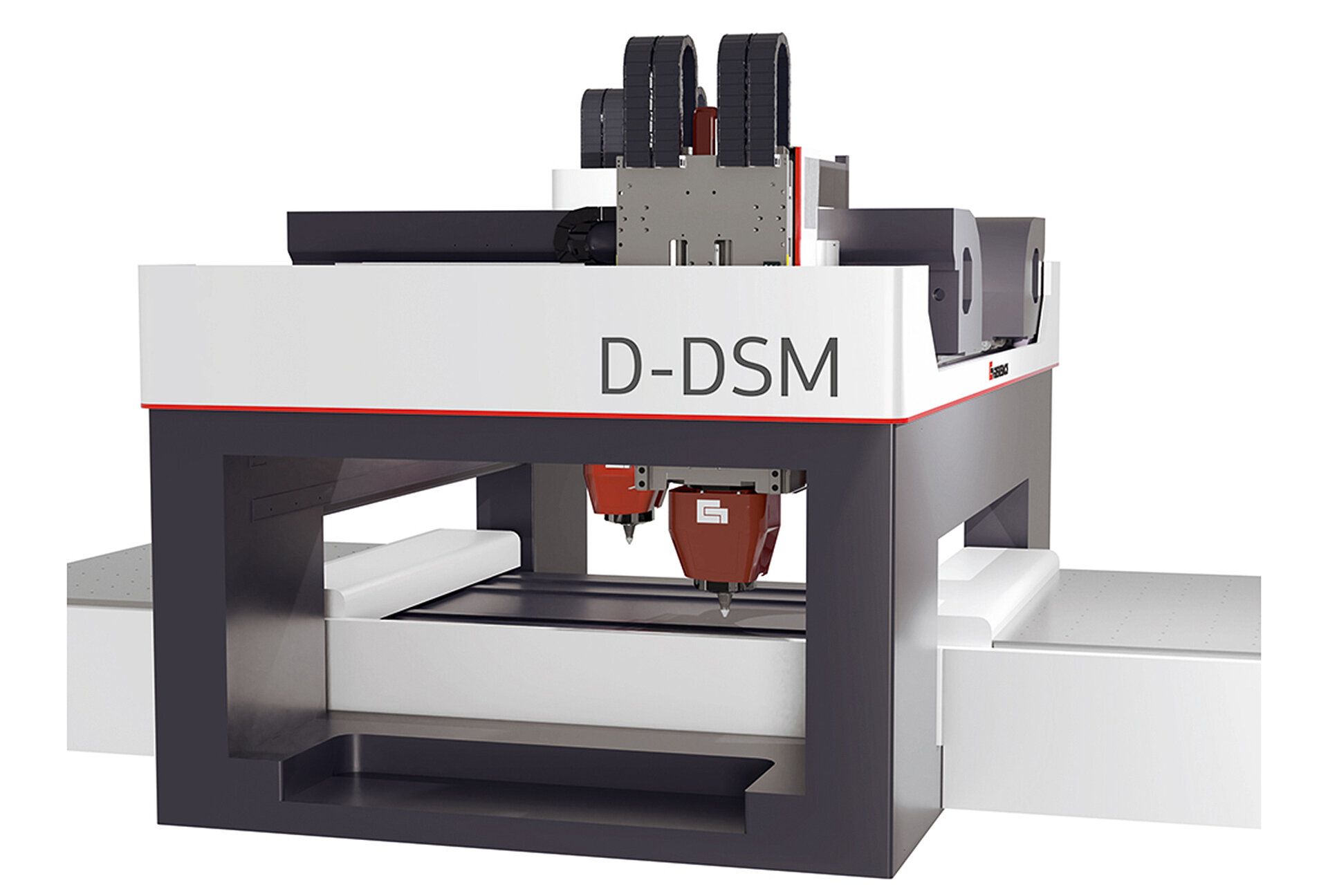