Friction Stir Welding with the DynaSTIR technology, a plus in aluminum processing
Reduced process forces, minor costs
As a system integrator and provider of Friction Stir Welding equipment with many years of experience Grenzebach offers both complete FSW process solutions for industrial serial production and continuously works on innovative solutions. This facilitates multi-part DynaSTIR tools and the new DynaSTIR welding head generation to significantly reduce the typically high process forces for the friction stir welding - frequently more than 50% compared to the use of conventional friction stir welding tools. “This leads to new application fields for the joining technology. Components, materials and the machine are significantly relieved by use of the DynaSTIR tools. The material thickness for light-weight construction can additionally be significantly reduced, even for components with reduced stiffness, for example battery housings in automotive light-weight construction. This way, users in all industries can once more save material, weight, and manufacturing costs", emphasizes Michael Sieren, head of sales for the Friction Stir Welding technology at Grenzebach.
The cream of the crop when it comes to tightness
Tightness is an indispensable aspect for light-weight design and components such as battery housings and battery trays, cooling plates, power electronic housings and heat exchangers or coolers. Long-term, firm, media and pressure-tight connections are “a must". During friction stir welding, which is a welding procedure being performed without melting, no pores or heat-cracks are generated. These effects can be the frequent root cause for leakages in the case of conventional fusion welding. This effect is increased when mixed compounds made of aluminum and casting alloys, which is by now a standard for many designs and components of liquid-cooled systems in the automotive sector, come in to play.
Components keep in shape
Hybrid structures and thin metal sheet applications have significantly increased, especially in automotive light-weight construction. Within the frame of E-Mobility the demand for battery housings and support structures, which are typically welded from thin-wall extruded aluminum profiles, has strongly increased. Another example: Flat plate heat exchangers with very thin wall thicknesses which are used for cooling of electronic components such as frequency converters or battery modules in electric and hybrid vehicles.
In the case of welding-technical manufacturing of these products, the tendency for distortion of the used aluminum material is frequently another challenge. In this context, the DynaSTIR technology is able to increase the performance of the FSW. Obviously, this is realized at the fair booth by means of a solar collector made from aluminum molded parts, each with wall thicknesses of 1 mm in the lap joint with process forces of a mere 900 N. By means of the reduced heat input of the DynaSTIR tools, the molded parts can be welded with low distortion. The finished component is true to dimension even without post-finishing.
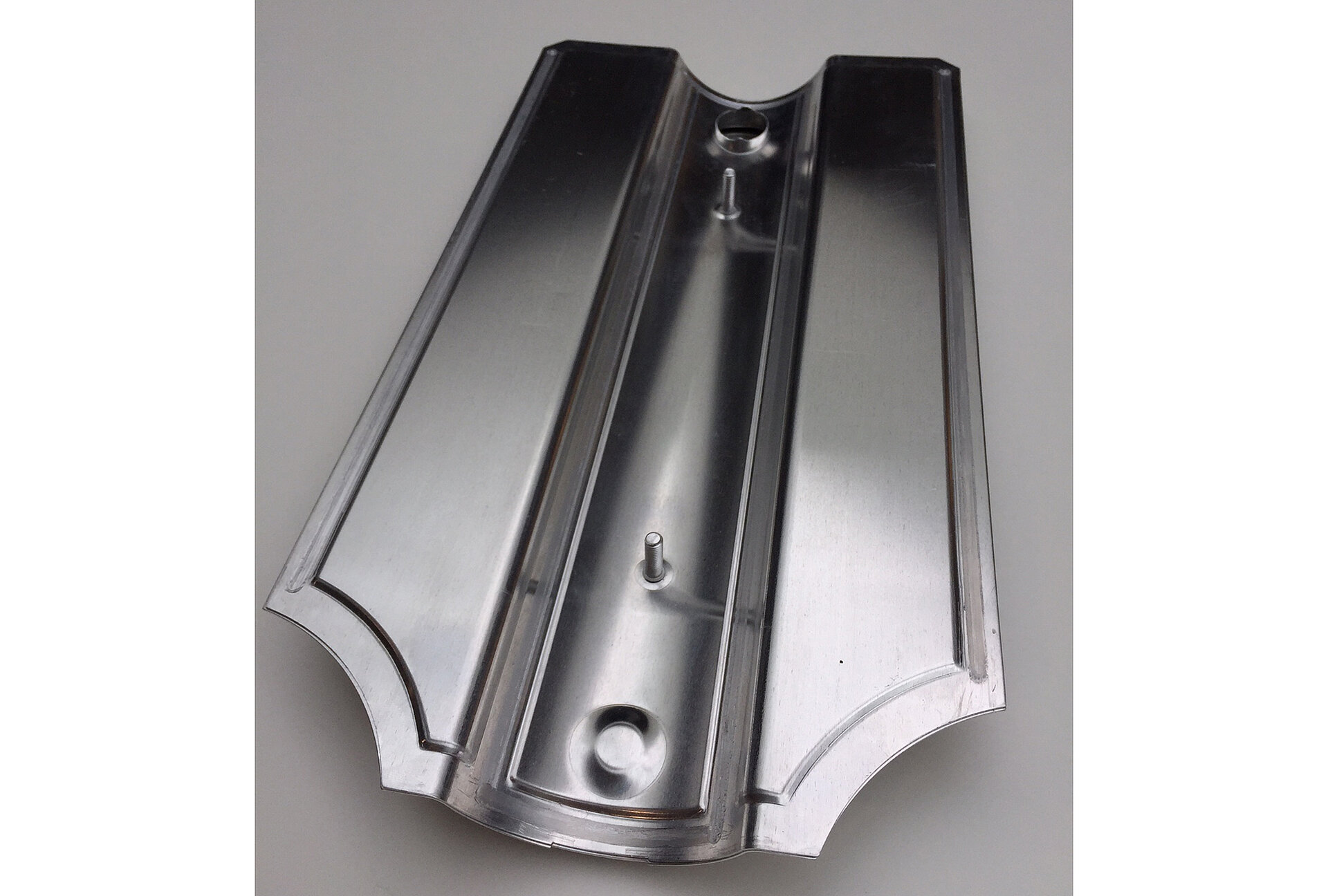