Friction stir welding technology for green mobility
Cars powered by green electricity are speeding – the automotive industry is on the rise. Politics provide strong impetus for low-emission vehicles at ever shorter intervals. California, for example, is planning to ban combustion engines starting 2035. Germany as well is discussing the end of the combustion. The EU's climate protection target of a 40 percent reduction in CO2 emissions by 2030 could be increased to 55 percent. Car manufacturers are restructuring their portfolios accordingly focussing emission-free drive solutions. Concepts, such as driving on electricity have a direct impact on the aluminum usage in the supplier industry.
Orders from the automotive industry throughout Europe
"The demand for welding casting components for the automotive industry is growing drastically – for example in the production of battery trays and heat exchangers for electric vehicles. This is where our friction stir welding process can make a difference," says Sahin Sünger, Product Manager FSW at Grenzebach. In 2020, the company has already received several big orders from European car manufacturers that rely on friction stir welding for e-mobility and related components. Grenzebach offers FSW solutions for battery trays in cast and extruded construction for hybrid and BEV (Battery Electric Vehicle) models. Additionally, Grenzebach is represented in the market with FSW solutions for heat exchangers and power electronics. With this, Grenzebach supports renowned Tier-1 companies worldwide in creating a technological pole position for automotive manufacturers (OEMs) with the components they produce.
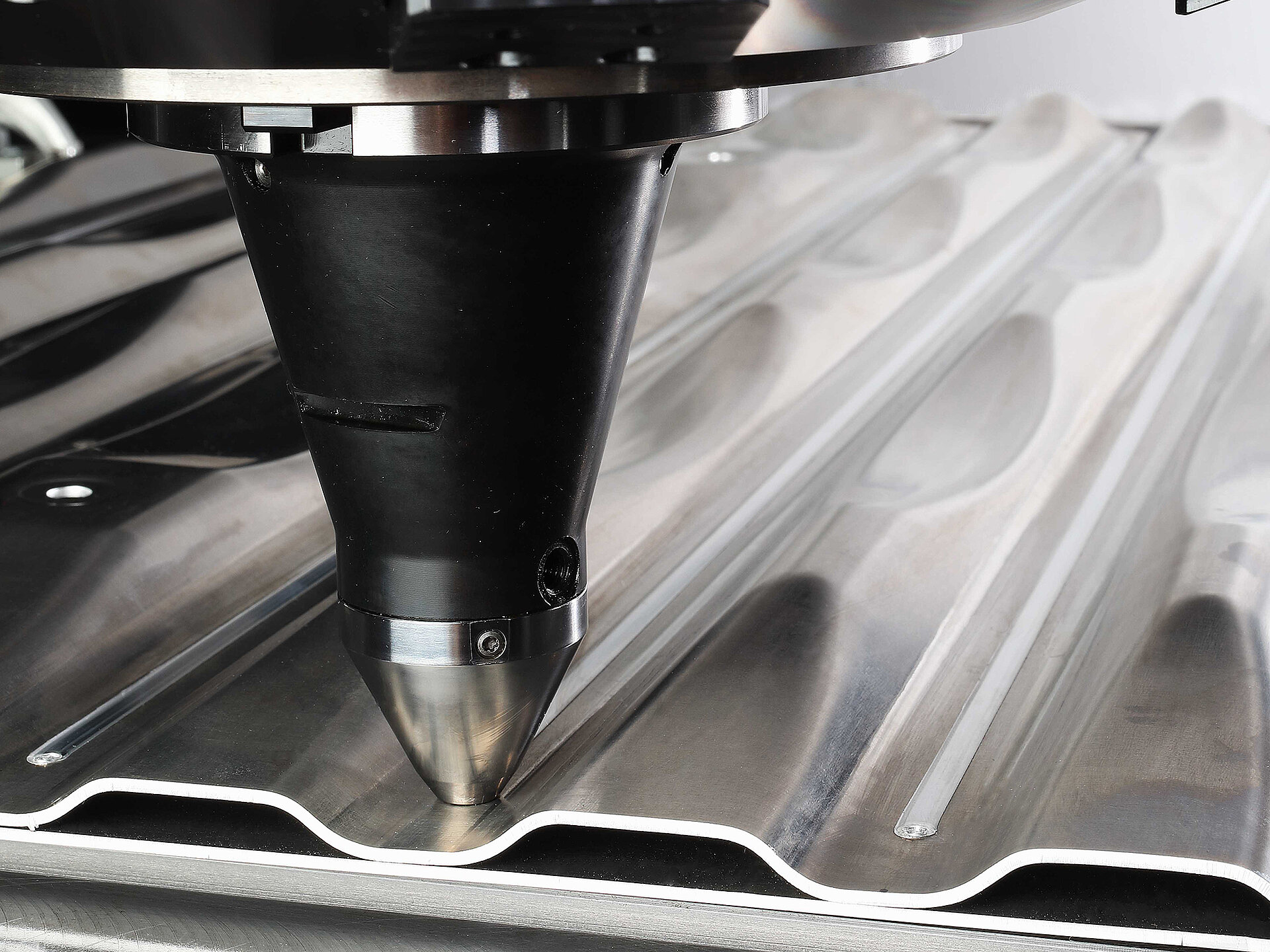
Friction stir welding is low-emission and creates robust welding seams
This often involves working with porous castings and uneven surfaces that are difficult to process when using conventional welding techniques. This is where friction stir welding can play out its strengths. A rotating tool generates the required process heat through friction and pressure at the welding seam. The heated material becomes malleable and is stirred by the rotation of the tool along the seam. The seam created is characterized by a special tightness. The result is a homogeneous structure with excellent properties. Because the sealing seam is also extremely resistant to mechanical stress, it can be used at structurally relevant points. The high loadbearing capacity of the FSW seam significantly contributes to the safety of the vehicles.
The joints created by FSW are low-distortion due to the low energy input. Last but not least: emission-free processes meet low-emission drive technologies.
Compared to conventional fusion welding processes, such as arc welding, friction stir welding requires neither welding rod nor shielding gas or complex exhaust systems. Furthermore, the application is low-noise and does not generate any optical radiation.
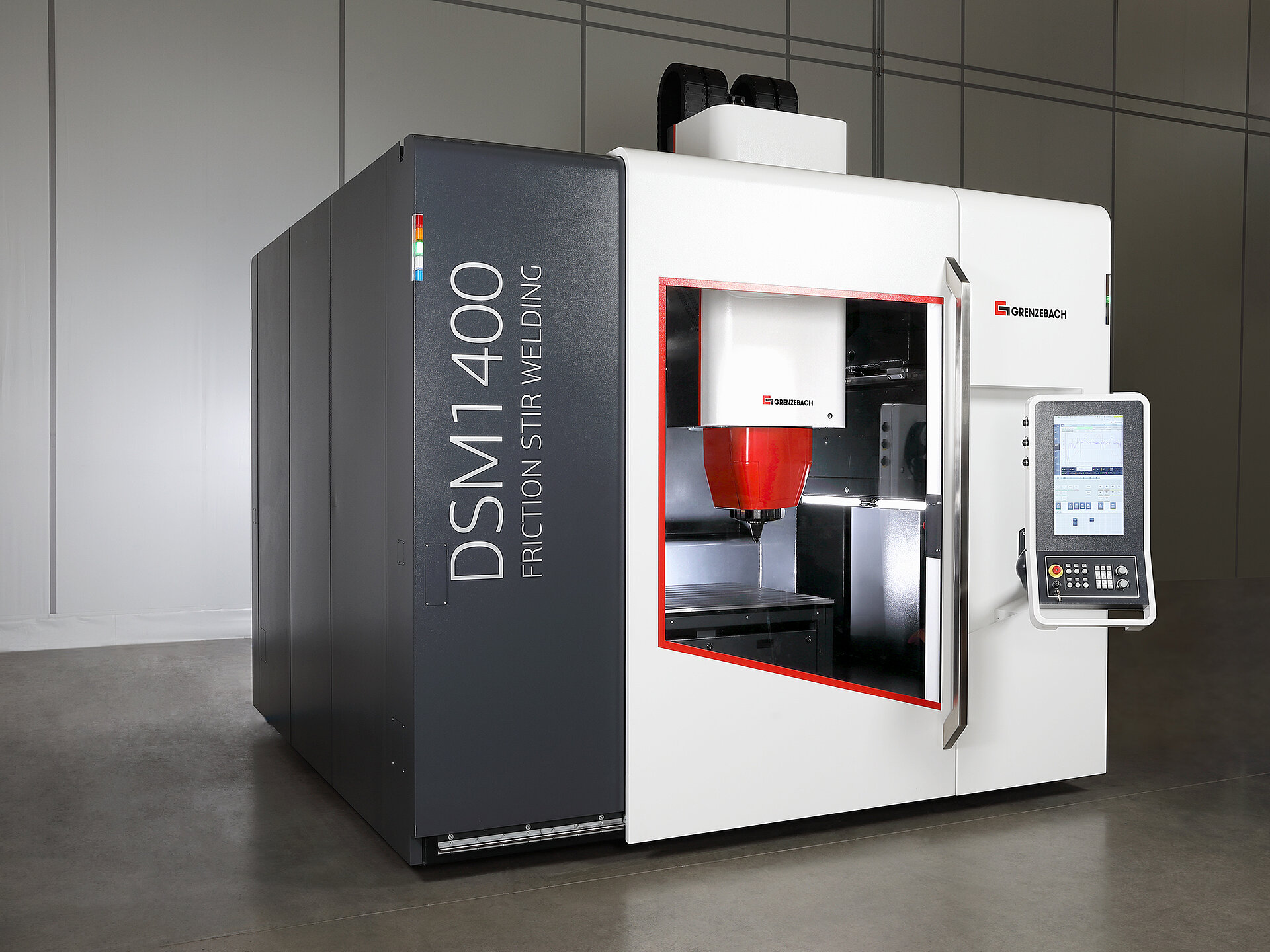
Our experts continuously develop innovative technology
Grenzebach has gained experience with the technology and its advantages in a wide variety of projects. The company makes its in-depth knowledge of friction stir welding and its comprehensive practical expertise available to its customers through continuous improvements. Together with product developers and process experts on the user side, Grenzebach's specialists are continuously developing FSW technology and offer a broad portfolio that can be customized to any market requirements. Various system concepts are available – from gantry systems with customer-specific work areas to robots that weld 3D geometries. "Our new D-DSM double-spindle system, which we showcased at the Automotive Engineering Expo in 2019, is already being used for the high-volume production of battery trays for electric vehicles. We hit the nail on the head and meet the needs of the industry while we continue to develop the portfolio with foresight," emphasizes Sahin Sünger.
High development and production penetration, reliable partner
As a technology supplier, Grenzebach supports the change in mobility. The order intake from the automotive industry for FSW services is very good. At its headquarters in Hamlar near Augsburg, Grenzebach is equipped with a high level of development and production depth for FSW technology. "We are a well-positioned family owned business that has been a global player for years. On this foundation, we show the highest performance even in times of change and uncertainty. Our FSW team lives a high degree of agility, we take up impulses for innovations early on and with enthusiasm", says Christian Herfert, Head of Friction Stir Welding Technology at Grenzebach.
We have an eye on product design and processes The Grenzebach portfolio is rounded off by customer-specific component supply technology for integration solutions and MES connections. Christian Herfert: "The holistic view of projects and customer questions has always distinguished us. From the very first idea, we provide advice on product design and process management and offer the high-performance equipment needed to do this".
Excellent technology
Grenzebach has already received a number of awards for its innovative strength in FSW technology: this past summer, the company received the igus vector award for increasing the functionality of the FSW portal system by using the igus system. This specific solution for the energy supply unit enables the welding head to be turned by +/- 720°. A decisive feature for welding complex geometries, such as heat exchangers. Grenzebach and its software partner Weidmüller had already received an award from the trade journal elektro Automation at the beginning of 2020. For the realtime quality control supported by artificial intelligence (AI) for friction stir welding in industrial production. "The awards and the strong claim from the e-mobility industry
inspire the whole FSW team. We are committed to developing the processes and products of tomorrow," says Christian Herfert.
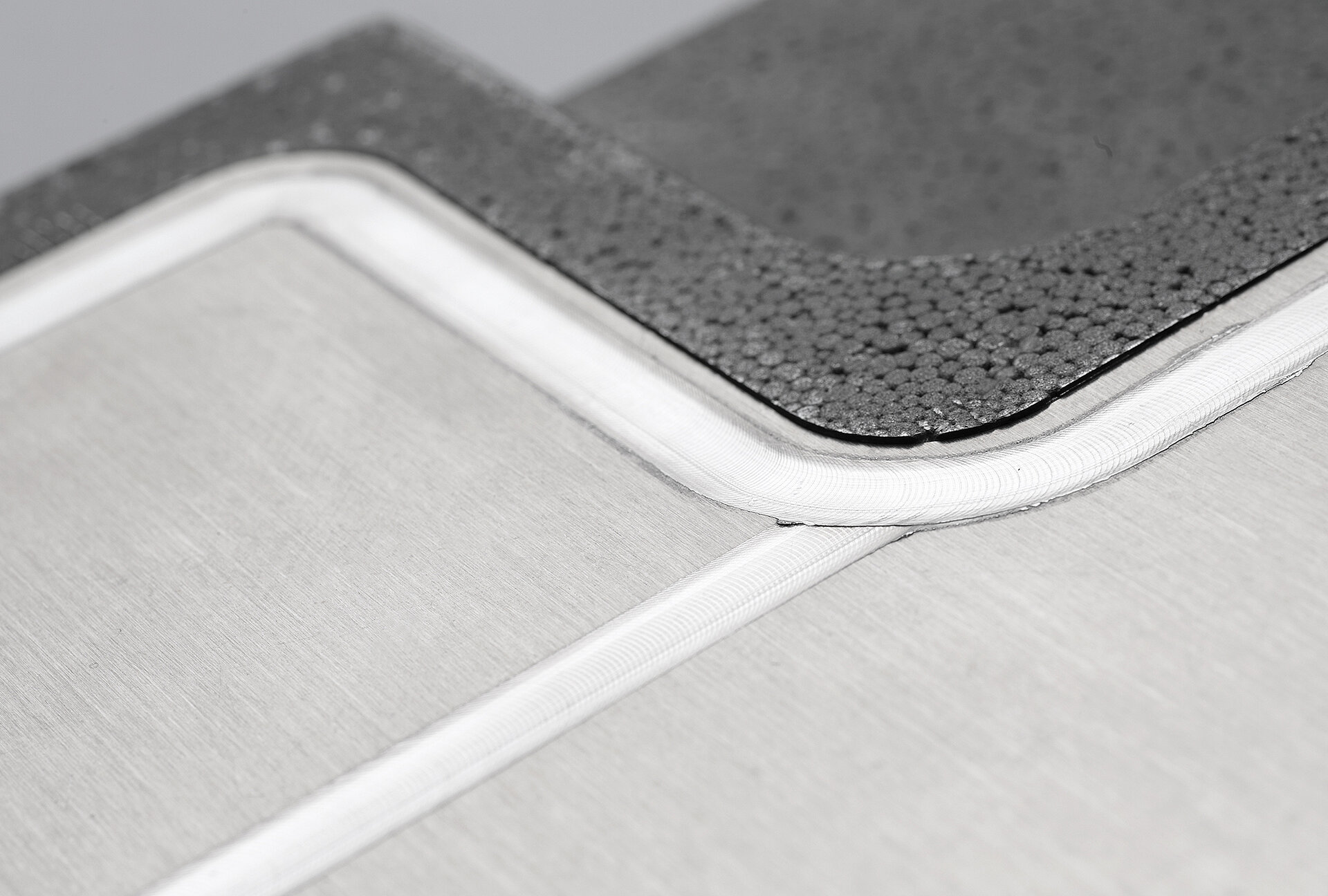