Development of an optical measuring system for grinding processes and more
- Development of an optical measuring system for a leading supplier of grinding and finishing systems in the wood-based panel industry
- Measuring roughness values and chatter marks during the running production to avoid B-goods
- Solution can also be applied to other industries
A leading grinding and finishing systems provider for the wood-based panel industry approached Grenzebach with a specific request: They were looking for a functioning sensor technology for the detection of chatter marks and roughness on the surfaces of sanded chipboard, fiberboard, OSB and plywood boards. After several attempts by other companies failed to provide a solution, we, as an experienced digitization and development partner to the wood industry, were able to convince that we could develop the requested optical measuring system.
Request for optimized process control
This request was based on the customer's wish to offer automated grinding production. Conventional wide belt grinding machines, however, do not provide any information about the quality of the ground surface. Plates are usually rejected and manually inspected for roughness and chatter marks. Therefore, the customer wanted an optical measuring system that automatically provides information on shapes and distances of chatter marks as well as surface roughness, since it would serve to optimize process control in several ways:
- Ideal machine setting to reduce energy and operating costs
- Correct insertion of the grinding belts to save resources
- Easy operation of the machine by collecting and displaying process data
- Quality control and documentation for a better production overview
- Early detection of worn-out grinding belts
The aim was to identify the characteristics from the facts supplied from which the operator would be able to derive appropriate measures (e.g. changing the grinding belts) to prevent rejects. Therefore, the solution system is essentially a preventive measure that is not aimed at subsequently sorting out low-quality goods but rather at preventing them from arising in the first place. Thus, it is a process monitoring system that issues an early warning before the tolerances for B-goods are exceeded. That allows the customer to intervene preventively in the grinding process to enable quality at any time.
Optical measuring: chatter marks and roughness
The optical measuring system for wide belt grinding machines developed by Grenzebach focuses on two characteristics:
- Surface roughness: grinding should only be as fine as necessary to reduce wear, prevent extended idle times and optimize quality. Based on the collected roughness values, it is possible to determine whether individual settings have been selected correctly. In addition, the roughness is heavily dependent on the idle time and condition of the grinding belts.
- Chatter marks: early detection of worn grinding belts or bearing damage can prevent the production of rejects. The basic challenge in detecting the chatter marks is the difficulty in detecting them in the uncoated raw plate. Furthermore, the increasing process speeds (up to 120m/min) do not even allow a hundred percent evaluation of the ground surface.
The solution: intelligent optical measuring system
Using a multi-stage process including test phases, development of root cause detection algorithms and installation of a prototype, we developed a camera system for surface inspection that measures both roughness and chatter marks and passes these measured values to the central control software. All relevant data and information run together here throughout the entire grinding process and are analyzed. Specific parameters and threshold values can be adjusted and continuously optimized so that the plates are always ground in the ideal range. This enables consistently high quality and reduces the costs of maintenance.
The first tests were already conducted in 2015. The prototype was installed in 2018/2019 and the first series type in 2020. The customer was so impressed with our measuring solution that they ordered five more systems.
During the development process of software and hardware, computer systems and measuring modules, each consisting of two illumination units and a camera, we had to face new challenges again and again. Because of the complexity of the project, maintaining good communication between us and the customer was enormously important. For this reason, there was an intensive exchange between us and the customer's project manager during the entire project cycle.
Conclusion: efficiency and quality control – across industries
The early detection of chatter marks helps to prevent the production of B-goods and sustainably increases the quality of the grinding process. The new measuring system for monitoring the roughness values increases the efficiency of the plant: By removing less from the plate, machine wear and energy consumption are reduced. It also reduces the workload on the staff, who previously had to check both features manually. The optical measuring system has taken the automation of the production process to a new level. Now, the inspection is not done manually after production, but automatically during the running production. The plant works significantly more efficient.
Not only did the customer benefit from the investment, but also did Grenzebach. Both, Grenzebach and the customer, filed patents for the new technology during the development process. We also see further potential in the sensor solution –across all industries: We are currently looking for other areas of potential application for the optical measuring system; initial trials are in progress. After all, even if the current use case is a specific field of application, other industries can also benefit from the basic idea and function of the technology.
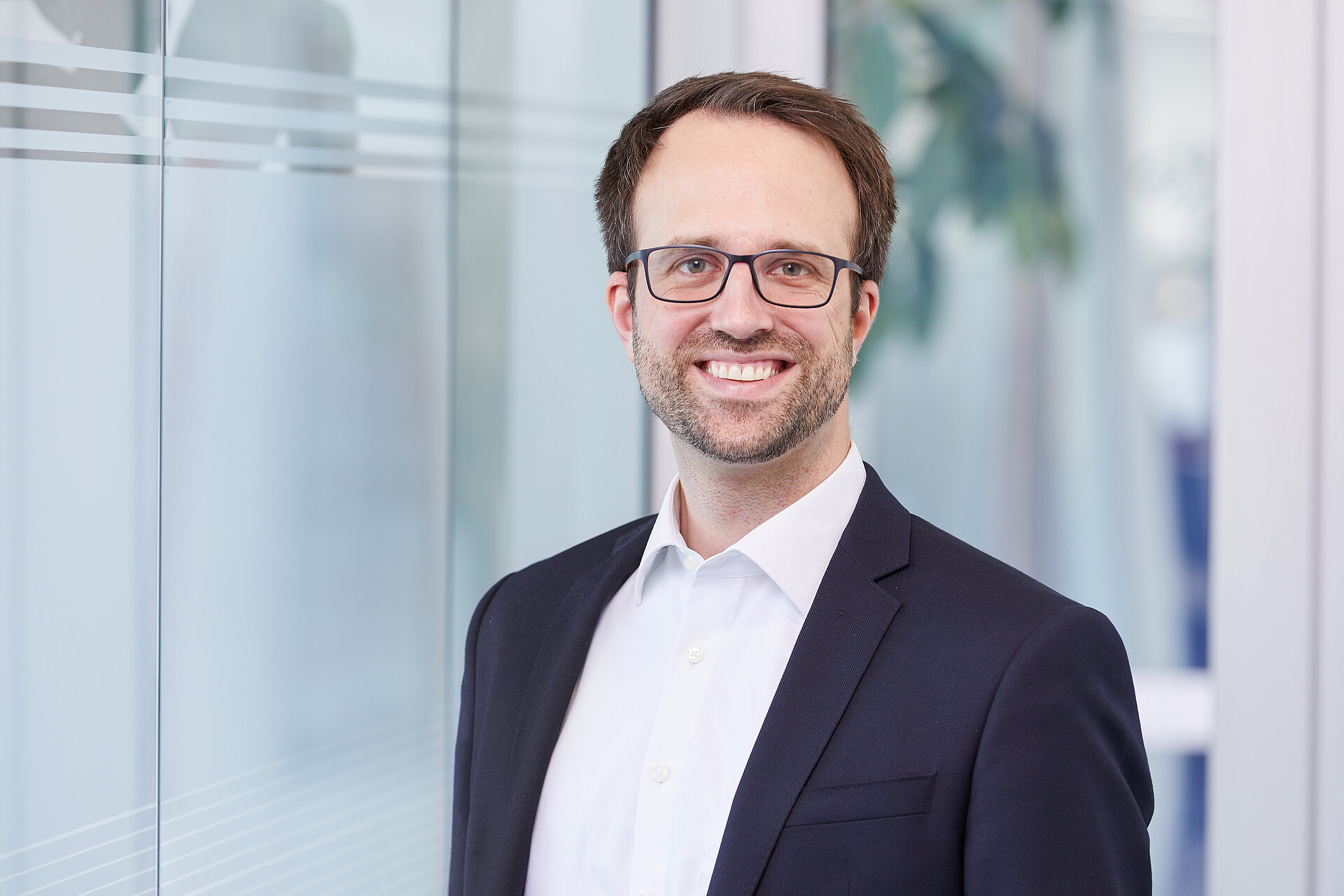