How intelligent automation and networking of printing and post-processing increase productivity in Additive Manufacturing
- The market for Additive Manufacturing (AM) processes continuies to grow
- With intelligent automation and networking of the individual AM process steps companies can save up to 70 percent of their manufacturing costs and make their AM fit for (large-scale) series production
- Grenzebach offers individual AM solutions: from single machines to holistic automation concepts
The market for Additive Manufacturing (AM) processes continues to grow and will even fivefold by 2030, according to SmarTech Analysis. More and more companies are taking a step towards the factory of the future because of the advancement of standardization in Additive Manufacturing at the industry level. Moreover, the advantages of Additive Manufacturing are convincing: lower inventory costs due to individual post-production of parts, a higher degree of specific product configurations, and flexible prototyping of complex geometries.
Nevertheless, AM is still often found in prototyping, small batch production, or as a supplement to mass production lines. The main challenge still lies in the long production time of a component in the AM system, whereas upstream and downstream production steps have significantly shorter cycle times. But companies that start right here can save up to 70 percent of their manufacturing costs and make their AM fit for (large-scale) series production. How? With intelligent automation and networking of the individual AM process steps using state-of-the-art transport, handling, and software technology. In this way, companies enable an optimal flow of materials, lower cost per part, and a safer working environment for employees.
Four reasons for automation
1. Increased efficiency and productivity
Due to automation, the printing process is intelligently networked and synchronized with downstream process steps (post-processing) that have significantly shorter cycle times. A practical example: while the part is still being printed in system 1, the finished build job of system 2 is already transported to downstream stations such as unpacking and inspecting; system 2 can already start the next print. No manual intervention is required, so production can also continue even though operators are not on duty.
Furthermore, there is no idle time – on the line as well as on the machine side. Employees can concentrate on more demanding tasks during the shift.
2. Lower cost per part
Intelligent networking of the individual production steps allows companies to make maximum use of equipment. Companies enhance the workload of all equipment along the process chain and avoid unnecessary investments. For example, automation enables machines to be used in three-shift operations, even though only one or two shifts are staffed with employees.
In this way, companies not only optimize their production times and machine utilization (OEE) but ultimately even produce at lower costs per part.
3. Enabling occupational health and safety
During the post-processing of 3D-printed parts, there are health risks due to fine dust exposure and the handling of hot objects. Using automated guided vehicles (AGV) with suitable sealed transport solutions, customized interfaces and machine fittings, and installed conveyor lines, the dust exposure for employees and the risk of injury from hot objects are reduced.
4. Repeatability and reproducibility
By always carrying out individual process steps, in the same way, the undesirable influence on the often still sensitive manufacturing process is minimized. The path is cleared for 24/7 series production and a light-out factory.
Intelligent automation and networking with the right partner
Networking the various working steps in AM processes is essential for a successful factory of the future. Moreover, it is fundamental to have a reliable and experienced partner at the side to master the challenges of additive series production. Grenzebach is the ideal partner for automating and networking individual process steps in powder bed-based Additive Manufacturing. Together with leading manufacturers of industrial 3D printers and post-processing equipment, Grenzebach develops individual solutions: from single machines to holistic automation concepts. Customers benefit from Grenzebach’s wide range of transport, exchange, bin picking, depowder, and combined, digital solutions – for higher efficiency and smooth workflow.
Grenzebach is also active as a partner in research projects such as NextGenAM and Polyline. The latter focuses on the Additive Manufacturing series production of plastic components. Here, the company contributes automated hardware and software interfaces as well as holistic solutions for material flow and transport between the individual processes.
With production sites in Germany, Romania, the US and China, as well as additional worldwide service locations, Grenzebach offers global on-site customer support and contact.
Meet Grenzebach experts – digitally or on-site
Companies can meet the AM experts of Grenzebach and explore the company’s latest automation solutions at any time: customers can arrange an individual guided tour through Grenzebach’s dynamic and innovative ‘365 days Grenzebach World’ in Hamlar (Germany) – digitally or on-site – to get to know the latest automation solutions for 3D technologies.
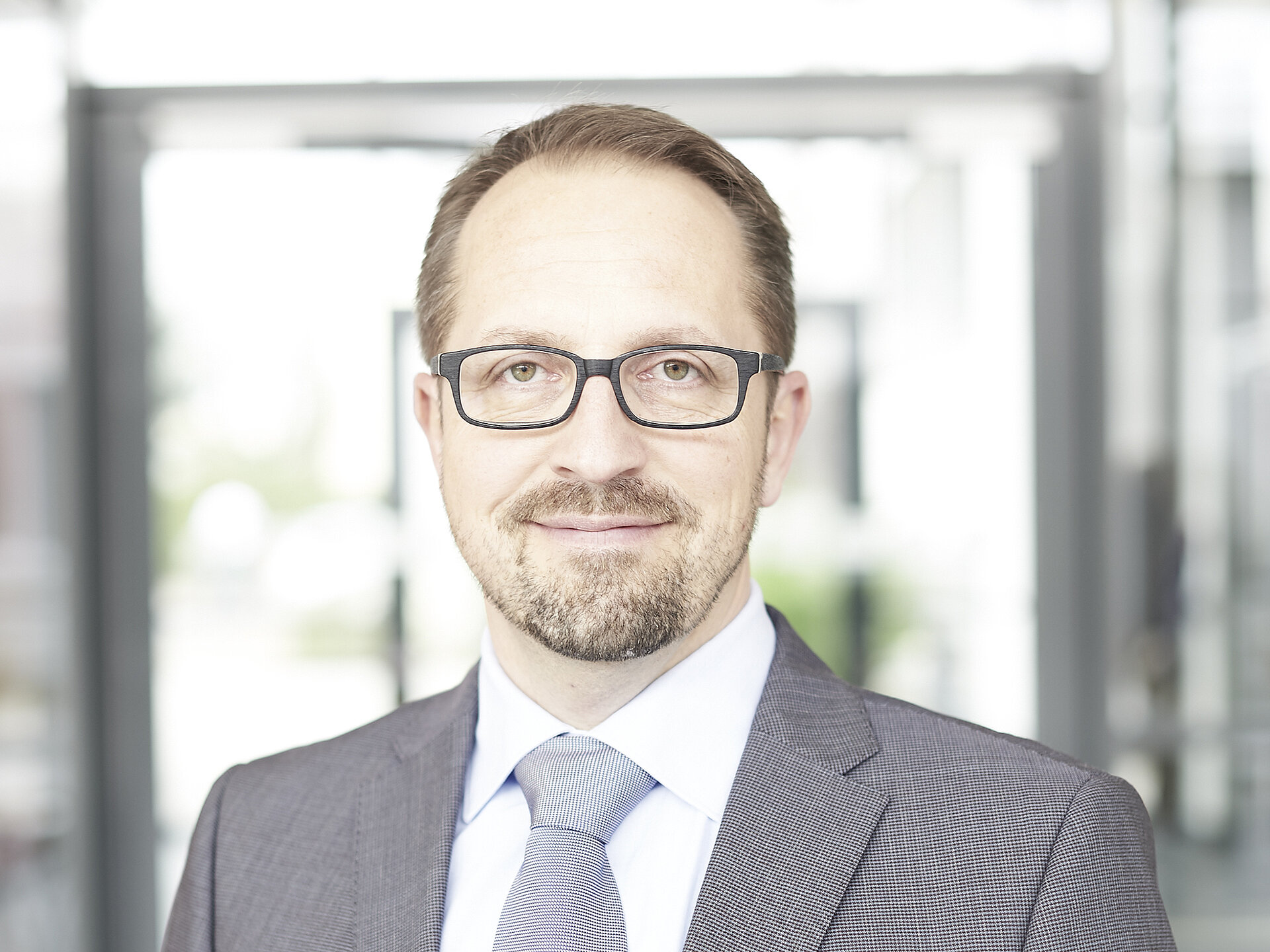