A rapid deployment force for glass production
- Float glass production plants must run reliably around the clock.
- Grenzebach provides its customers worldwide with seamless service to make this possible.
- In the future, a digital hub will further expand and improve this service.
HAMLAR, STOLBERG, OSTERWEDDINGEN/Germany. In hardly any other industry does the motto “time is money” hit the mark as much as in glass production. Plants run around the clock 365 days a year. This demands absolute reliability because every hour of downtime costs a huge amount of money. Maximum availability is therefore one of plant operators’ most important expectations.
For this reason, it is essential to have a partner on hand who can restore availability immediately and smoothly in the event of a malfunction or plant shutdown. Grenzebach, headquartered in Hamlar, Bavaria, has built up an internal service infrastructure to solve problems of any kind as quickly and effectively as possible. Customers are offered a service partnership over the plant’s entire lifecycle – with everything you could possibly expect from it. These are, first and foremost, constant availability thanks to a hotline and professional support from excellently trained, specialized technicians.
24/7 readiness for customers worldwide
This service team is available at Grenzebach around the clock, seven days a week – for customers worldwide. If there is a malfunction or any other challenge, everything is immediately set in motion so that the plant is up and running again as soon as possible.
The fact that this comprehensive service promise is kept is shown by statements from customers who have experienced Grenzebach’s service in action and have nothing but high praise for it. In 2021, for example, the people at Saint-Gobain Stolberg had an excellent experience with Grenzebach’s service after they were surprised by a flood and needed immediate help:
“In 2021, we had an immense flood in Germany,” says Dr. Christoph Schmitz, Plant Manager at Saint-Gobain Glass Deutschland GmbH in Stolberg (Rhineland). “The water was 50 cm deep in our control cabinets. We were forced to shut down our production. The Grenzebach service team was on-site very quickly to assess the damage and took action immediately afterward: motors were replaced and other spare parts delivered. After the repair, the plant was back in operation in only five weeks.”
Erwin Schwertberger, Service Manager at Grenzebach, who looks after this customer, recalls: “It was a pretty disastrous situation for Saint-Gobain, but our people did everything they could to restore production capability in the shortest possible time. I’m proud of the team.”
This is another advantage of Grenzebach’s service: in their personal service manager, each customer has an experienced expert at their side to provide long-term individual advice. In this way, glass producers are not only optimally protected against breakdowns but also optimally prepared for changing market requirements or necessary modernizations due to discontinuations. You could not ask for a better return on investment.
The Grenzebach service portfolio: available at all times via the hotline
The service team can be reached quickly and reliably from any part of the world with the phone hotline. Since the technicians have remote access to each plant, problems can often be solved directly and immediately. The current guaranteed standard response times for Grenzebach service contract customers are one hour until the technician calls back and a maximum of two hours until he or she remotely accesses the plant. In the vast majority of cases, the process is even faster.
Depending on the type and severity of the problem, a 3-level process is applied:
- 1st level: The service technician solves the problem on the first call via remote access. Around 90 percent of service tickets can be successfully handled at this level.
- 2nd level: If, contrary to expectations, level 1 support does not resolve the issue, Grenzebach Engineering intervenes with additional expertise and, if necessary, the deployment of specialists on-site.
- 3rd level: If the engineering department is unable to resolve the issue, the customer receives support from Grenzebach’s development department.
Spare parts are on-site in the shortest possible time
Especially at high levels, a lot depends on a smoothly functioning spare parts supply. Grenzebach also takes care of this: smart warehousing with lean, system-supported processes enables high spare parts availability and short delivery times in most areas of the world. Due to the new “Fast-Lane,” critical spare parts can now be delivered to any location in just a few days.
The future: digital support via a central hub
The service customer portal my.grenzebach.com will provide customers with a digital hub for service in the future. On this central platform, they can find an overview of their glass production plants, exchange information, make inquiries, and obtain quotes. They can post service tickets, upload images, and view current status and a history of service tickets. Also included are a digital spare parts catalog and a “document repository” for instructions, documentation and video tutorials. Grenzebach offers video tutorials that illustrate the design and operation of the systems and components for various technical topics, such as changing conveyor gearboxes or graphite blocks in a tin bath.
Florian Nagler, Vice President, Sales Business Unit Glass at Grenzebach Maschinenbau GmbH summarizes the situation: “My colleagues and I see accompanying our customers as journey partners throughout the entire service life of a plant as a sporting challenge. And we want to do that better and better, even though the production lines already have very high availability. Everything can be improved, so we take every available opportunity for technological progress to help our customers even more effectively.”
The number of satisfied service customers is growing
The Grenzebach service offer is very well received by the company’s customers. Currently, most of the customers in the glass industry have opted for the service contract with the 24/7 hotline.
Jens Schmidt, Process Engineer, Cutting Line at AGC f | glass GmbH in Osterweddingen, Saxony-Anhalt, also has high praise for the Grenzebach service: “High plant availability is extremely important to us, which is why we have concluded a service contract with regular maintenance on the cutting technology and stacking technology – including a 24/7 hotline and training for our personnel. The result has been a very high availability since the plant was commissioned in August 2009.”
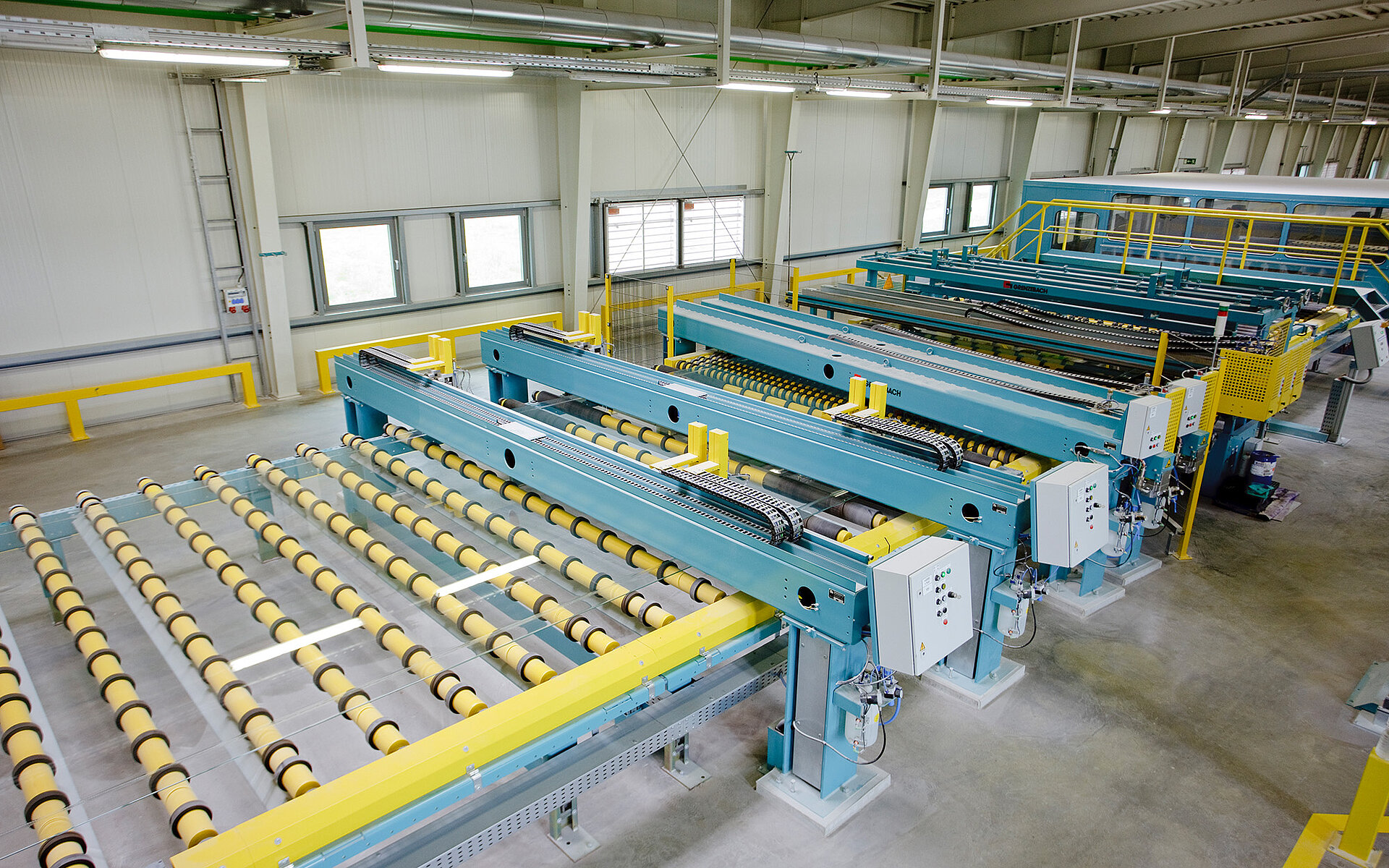